
The U.S. manufacturing industry, a powerhouse since its rise during the Industrial Revolution in 1820, has endured challenges from the Great Depression to the Great Recession. Today, at a time when business has become more global than local, manufacturers are faced with the ongoing challenge of staying ahead of ever-evolving industry standards and regulations, striving to maintain compliance while optimizing operations.
Consider Anheuser-Busch, a leading beverage company that has long prided itself on quality and tradition. Recently, the leadership team recognized that keeping up with evolving industry standards required more than just hard work and tenacity—it needed a technological overhaul. Navigating a complex and shifting regulatory landscape, managing extensive documentation, and ensuring consistent quality control are daily hurdles. The fast-paced global market demands agility and innovation, compelling manufacturers to rethink traditional approaches.
After investing in technology to improve work instructions and shift their SOPs from a traditional format to video SOP, Anheuser-Busch succeeded in decreasing employee time to proficiency by 80%.
To meet these advancing challenges, decision-makers and industry leaders are increasingly turning to artificial intelligence (AI). From predictive analytics to AI-powered video training platforms with AI quizzing, like that from DeepHow, the integration of AI in manufacturing not only optimizes operations but also plays a major role in ensuring that firms can keep up with the dynamic regulatory environment.
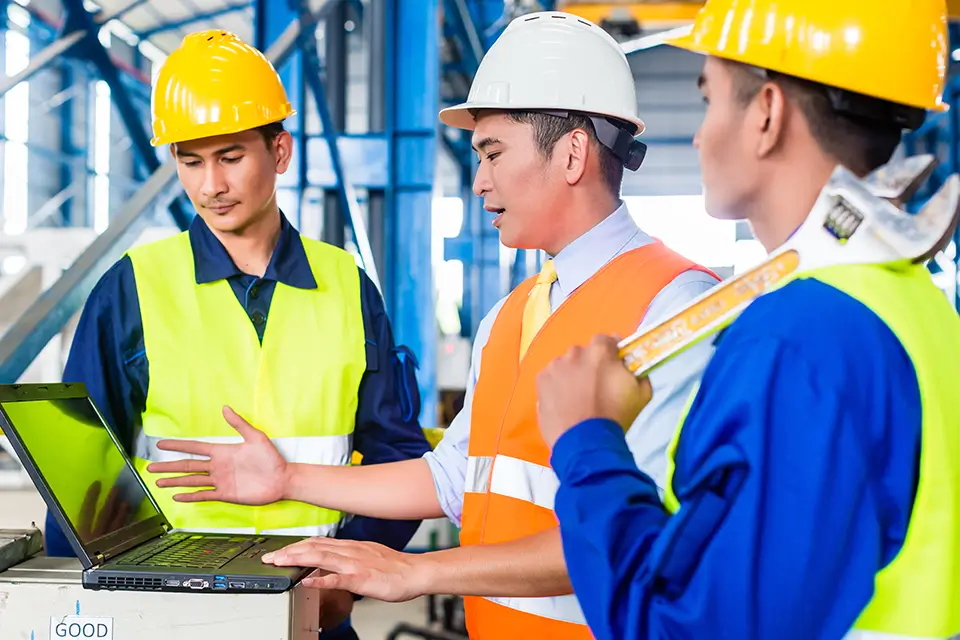
Navigating the Ever-Changing Industrial Landscape
Currently, manufacturing leaders are under immense pressure to meet the challenges posed by evolving industry standards. These standards are not static; they continually adapt to reflect advancements in technology, changes in regulatory requirements, and rising consumer expectations for quality, safety, and sustainability.
The International Organization for Standardization (ISO), for example, reviews its standards every five years and usually issues a new version three to five years later. These changes are often significant and are intended to be relevant to current best practices. Additionally, since 1981, the federal government has issued at least one manufacturing-related regulation each week, with the bulk coming from the Environmental Protection Agency (EPA). Safe and healthy working environments are ensured through regulation. However, the sheer volume of policies and inefficiencies in the process have increased the burden on manufacturing operations.
These evolving standards need continuous monitoring and adaptation by manufacturing firms. Failure to comply can result in hefty fines, reputational damage, and operational disruptions.
Traditionally, compliance has been managed through manual processes, which are often time-consuming and prone to human error. The complexity of regulatory requirements, coupled with the need for real-time data and rapid response, makes manual compliance increasingly impractical. This is where AI steps in, offering a smarter, more efficient approach to managing compliance.
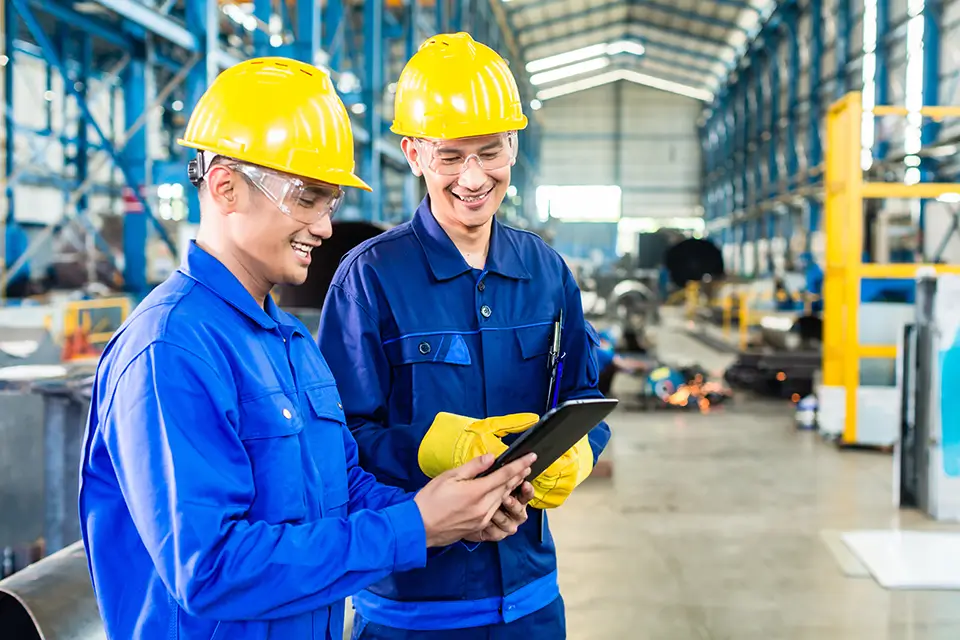
AI in Quality Control and Compliance
AI technologies, such as machine learning and predictive analytics, are revolutionizing quality control processes in manufacturing. By leveraging vast amounts of data generated on the production floor, AI can identify patterns and anomalies that human inspectors might miss. This proactive approach ensures that potential issues are detected and addressed before they escalate, thereby maintaining product quality and compliance with industry standards like ISO.
- Predictive Maintenance: One of the key applications of AI in manufacturing is predictive maintenance. By analyzing data from sensors embedded in machinery, AI can predict when a machine is likely to fail or require maintenance. This not only prevents unexpected downtime but also ensures that machinery operates within the required safety and quality standards.
- Process Optimization: AI can optimize manufacturing processes by analyzing data in real-time and making adjustments to improve efficiency and quality. For instance, AI can monitor production parameters such as temperature, pressure, and humidity and make real-time adjustments to ensure that products meet stringent quality standards.
- Regulatory Compliance: AI can also assist in regulatory compliance by continuously monitoring production processes and ensuring that they adhere to industry regulations. This includes tracking and documenting every step of the manufacturing process to provide a comprehensive audit trail, which is essential for regulatory inspections and audits. This includes analyzing and generating reports required for ISO certification.
- Training and Knowledge Sharing: AI-powered training platforms, like DeepHow, facilitate training programs for employees on the latest ISO standards and beyond. These platforms provide personalized learning experiences and ensure that all employees are up-to-date with compliance requirements.
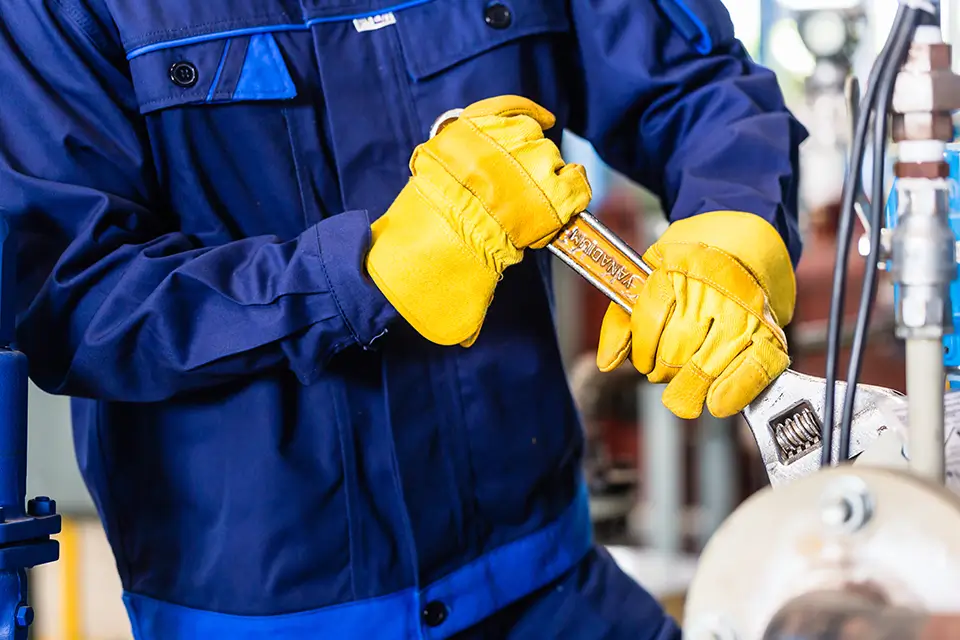
AI Quizzing: A Novel Approach to Training and Compliance
One of the lesser-known but highly effective applications of AI in manufacturing is AI quizzing. This innovative approach can help manufacturing firms stay agile and compliant with evolving industry standards and regulations by continuously updating training content and assessments. Among the benefits of AI quizzing:
- Continuous Learning: In a dynamic regulatory environment, it is crucial for employees to stay up-to-date with the latest standards and best practices. AI quizzing platforms can deliver personalized training content based on individual learning needs and progress. By continuously updating training materials and quizzes, AI ensures that employees are always aware of the latest regulations and compliance requirements.
- Assessment and Feedback: AI quizzing platforms can provide real-time assessments and feedback to employees, helping them understand their strengths and areas for improvement. This continuous feedback loop enhances learning outcomes and ensures that employees are well-prepared to meet regulatory standards while providing crucial data to supervisors and HR leaders.
- Data-Driven Insights: AI quizzing platforms can generate data-driven insights into employee performance and training effectiveness. By analyzing quiz results and training data, manufacturers can identify knowledge gaps and areas where additional training is needed. This targeted approach to training enhances overall compliance and operational efficiency.
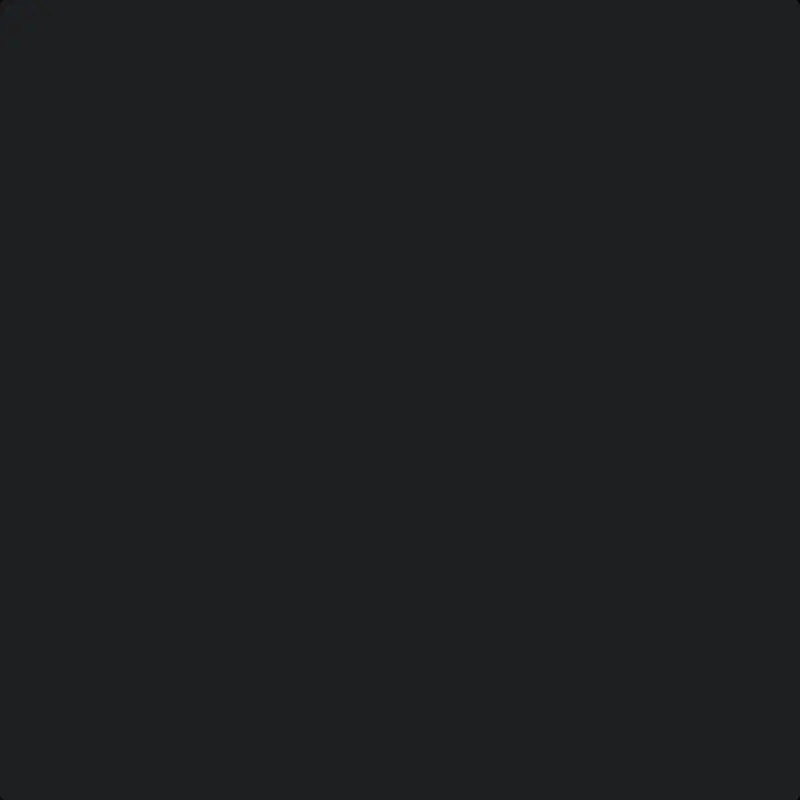
Implementing AI to Meet Evolving Industry Standards
According to a survey by the Manufacturing Leadership Council, almost all manufacturers expect to increase AI investments in operations by 2030, with 20% saying they expect investments to increase from 50% to more than 100% in the coming years. For manufacturing leaders and decision-makers, implementing AI to meet evolving industry standards requires a strategic approach. Here are some best practices to consider:
- Identify Priority Areas: Determine which aspects of your manufacturing processes are most impacted by evolving standards. Focus on these areas for AI implementation to maximize impact.
- Invest in Data Infrastructure: AI relies on data. Ensure you have robust data collection, storage, and management systems in place to support AI applications effectively.
- Collaborate Across Functions: Involve cross-functional teams in the AI implementation process. This ensures diverse perspectives and buy-in from stakeholders across the organization.
- Start Small, Scale Gradually: Begin with pilot projects in specific areas to test AI solutions and validate their effectiveness. Once proven successful, gradually scale up implementation across the organization. Target critical problem areas first and develop a robust suite of training content to meet them.
- Ensure Data Privacy and Security: Implement measures to protect sensitive data used by AI systems, adhering to relevant regulations and standards such as GDPR and ISO 27001. Prioritize technologies that make security a key part of their mission.
- Provide Training and Upskilling: Equip employees with the skills and knowledge necessary to work alongside AI systems. Offer training programs to build AI literacy and ensure smooth integration into workflows.
- Monitor and Iterate: Continuously monitor AI performance and gather feedback from users. Use this data to iterate and refine AI systems over time, ensuring they remain aligned with evolving industry standards.
- Stay Abreast of Regulatory Changes: Regularly monitor updates to industry standards and regulations relevant to your sector. Adapt AI systems accordingly to maintain compliance and mitigate risks.
- Embrace Collaboration and Partnerships: Leverage partnerships with AI vendors, industry associations, and research institutions to stay at the forefront of AI innovation and share best practices with peers.
- Cultivate a Culture of Innovation: Foster a culture that encourages experimentation, learning from failures, and embracing new technologies like AI. This mindset shift is crucial for successful AI implementation and adaptation to evolving industry standards.
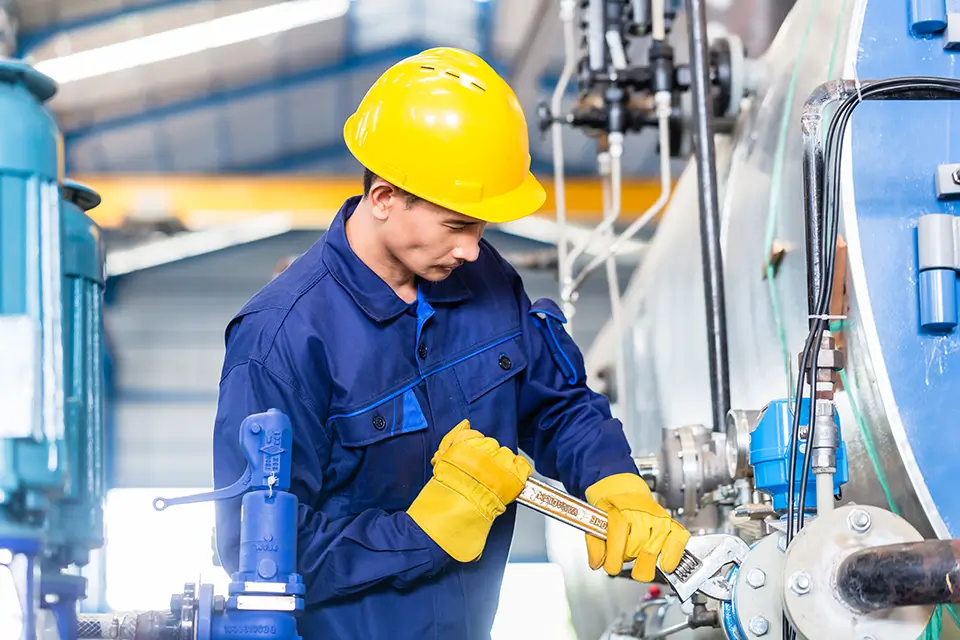
The integration of artificial intelligence in the U.S. manufacturing industry represents a significant leap forward in meeting the demands of evolving industry standards and regulations. As AI continues to transform quality control, predictive maintenance, process optimization, and regulatory compliance, manufacturers are better equipped to navigate the complexities of the global market. By adopting AI technologies and following best practices, industry leaders can ensure operational excellence, maintain competitiveness, and foster a culture of innovation. Embracing AI is not just a response to current challenges but a strategy for future success, enabling the manufacturing sector to thrive in a changing landscape.