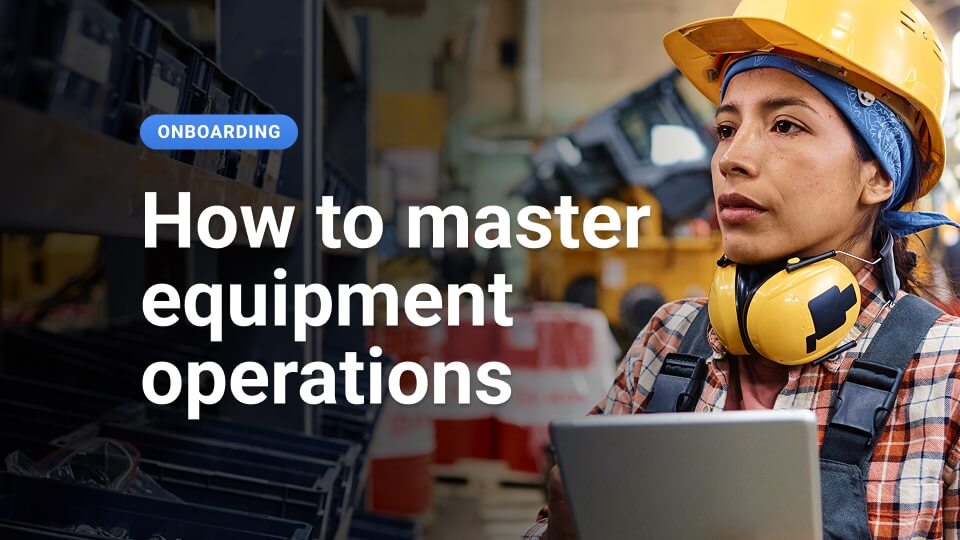
In manufacturing, frontline workers are the backbone of efficient equipment operation and maintenance. With retiring experts taking decades of knowledge with them, manufacturers face the dual challenge of closing skills gaps and training a new generation of operators quickly and effectively. This guide explores how modern tools—especially video-based Standard Operating Procedures (SOPs)—empower frontline workers to master equipment operations and drive operational excellence.
The Frontline Challenge: Skills Gaps and Knowledge Retention
Manufacturers face unprecedented workforce challenges:
- Retiring Workforce: Retirement waves are depleting institutional knowledge, leaving teams without critical know-how. In the USA alone, there are an estimated 12 million manufacturing workers over the age of 55.
- Inconsistent Training: Traditional methods like text-based SOPs or classroom instruction often fail to standardize knowledge across locations.
- Accelerated Onboarding Needs: As product cycles shorten, new hires must reach full productivity faster than ever.
The solution? Leverage video SOPs to transform training and knowledge sharing.
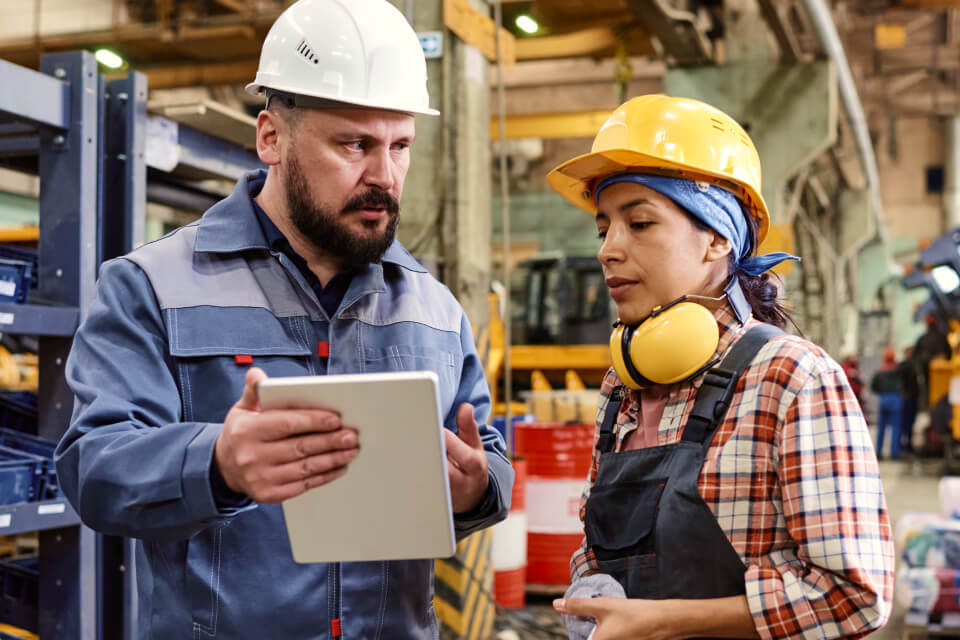
Why Video SOPs Are the Key to Frontline Empowerment
Video-based SOPs address these challenges head-on by providing an engaging, accessible, and scalable approach to training.
Improved Knowledge Retention
Studies show that people remember 80% of what they watch, compared to just 20% of what they read. Visual and auditory content accelerates learning by demonstrating tasks in real-world settings.
24/7 Accessibility
Frontline workers can access training videos anytime, reducing reliance on supervisors for guidance. Whether it’s troubleshooting at midnight or revisiting complex tasks, on-demand videos empower workers to act independently.
Enhanced Consistency
Standardized video SOPs ensure training is consistent across shifts, lines, and locations, eliminating variations in how tasks are taught and performed. For instance, subtle equipment differences between plants can be documented to ensure accuracy.
Time and Cost Savings
Video training requires 40–60% less time than traditional classroom sessions and eliminates travel and scheduling costs for in-person sessions.
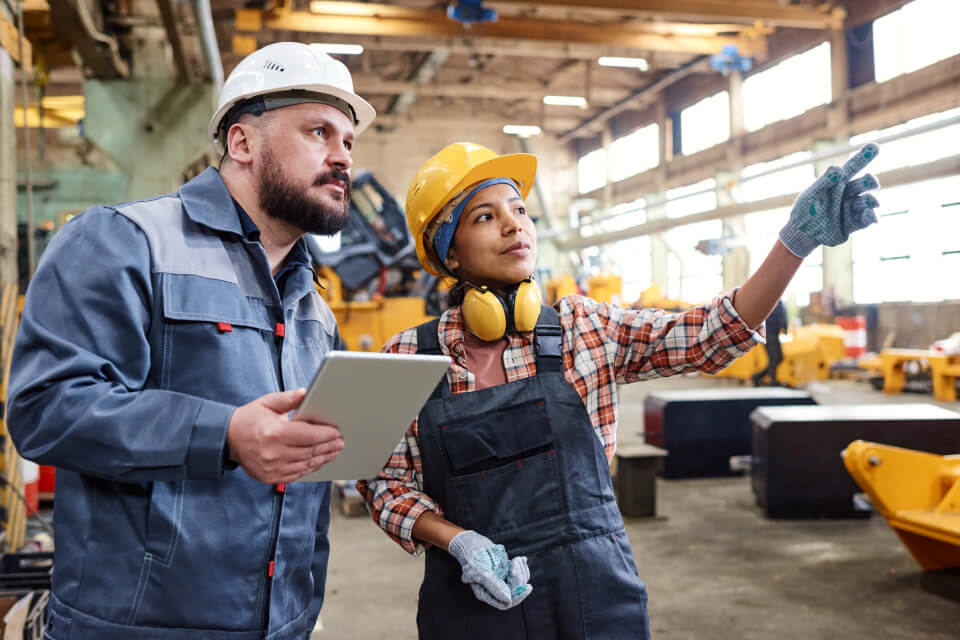
Real-World Impact: Success Stories from the Frontline
- Faster Equipment Maintenance: One manufacturer reduced cylinder replacement times from 3 hours to 45 minutes using video SOPs. Workers could review precise steps before starting, minimizing errors and improving uptime.
- Accelerated Onboarding: DeepHow customers report reducing onboarding time for new hires by 80%—from 538 days to just 125 days. This rapid upskilling ensures teams are production-ready in record time.
- Empowered Night Shifts: With video SOPs readily available, night-shift workers no longer depend on daytime supervisors for guidance, enabling quicker resolutions during downtime.
- Enhanced Safety Compliance: When one manufacturer reviewed a video SOP, they identified a missing safety guard on equipment. Addressing this oversight prevented potential injuries and reinforced compliance. When the frontline feels safe, their confidence and efficiency increases.
Actionable Steps to Empower Your Frontline Workforce
Manufacturing leaders can adopt these strategies to harness the power of video SOPs:
- Start with High-Impact Tasks: Focus on capturing video SOPs for frequently performed or error-prone tasks, such as equipment maintenance and troubleshooting.
- Keep Content Concise and Engaging: Create 3-5 minute videos for better retention and focus. Bite-sized content is easier to absorb and allows workers to revisit specific sections as needed.
- Build a Digital Training Library: Store videos in an easily accessible system and link them to QR codes on equipment or workstations for quick reference during operations.
- Involve Your Experts: Equip experienced workers with easy-to-use tools to record their knowledge. Their real-world insights provide invaluable learning material for new hires.
- Leverage Analytics for Continuous Improvement: Use data to track video views and worker feedback. Refine your content to address gaps or improve clarity based on usage patterns.
Why DeepHow is the Ideal Partner
DeepHow is revolutionizing training in manufacturing with AI-powered video tools. Features like multilingual support, automatic transcription, and seamless integration into existing systems make it easier than ever to create and distribute SOPs.
- Quick Creation: Produce videos in minutes for rapid deployment.
- Global Scalability: Translate SOPs into multiple languages with a click.
- Increased Engagement: Personalized content builds worker pride and a sense of ownership.
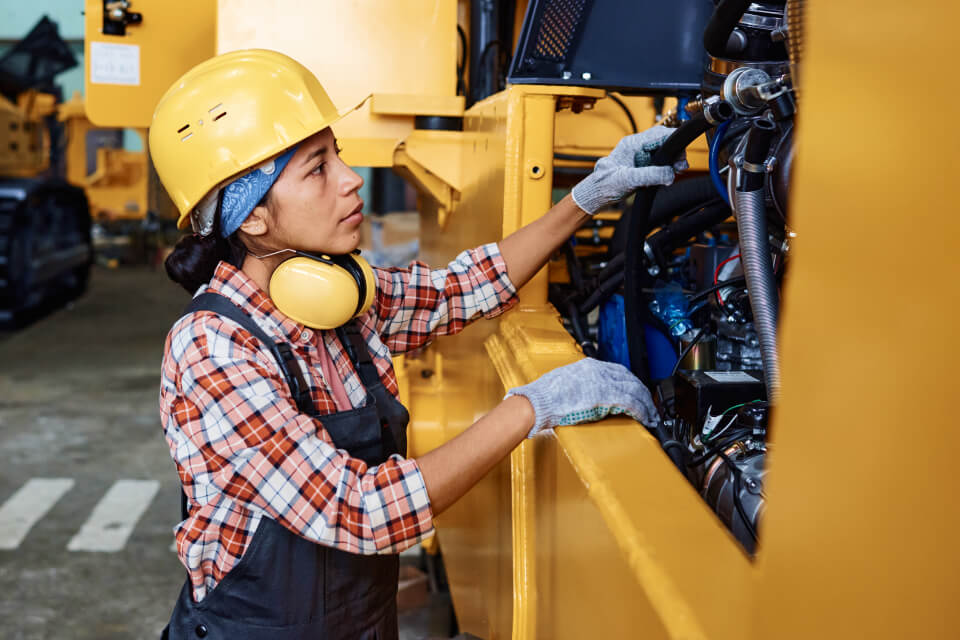
The Future of Frontline Empowerment
Mastering equipment operations is no longer a bottleneck for manufacturing success. By adopting video-based training tools like DeepHow, companies can empower their frontline workforce to operate confidently, reduce downtime, and enhance safety.
Equip your workforce with the tools they need to succeed. The investment in their skills today ensures operational resilience and excellence tomorrow.