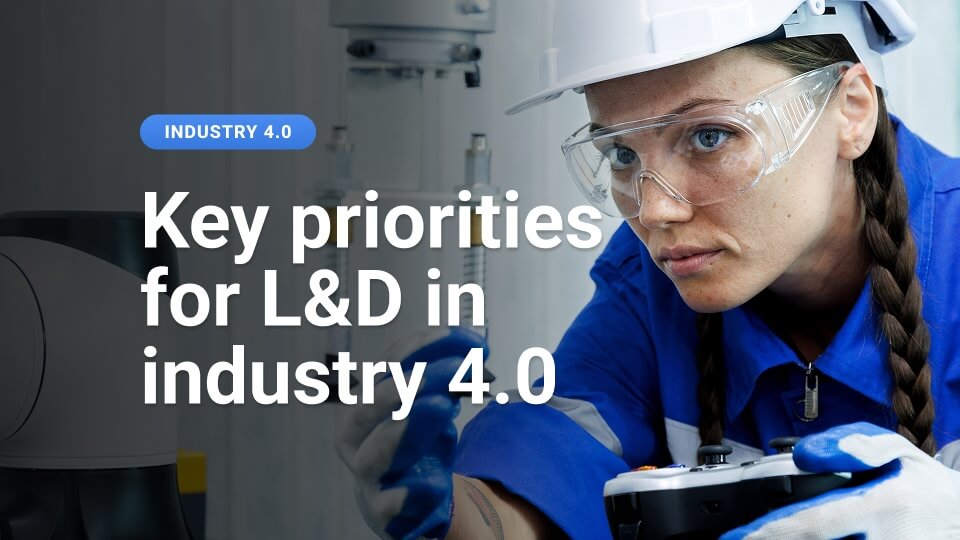
Collectively known as Industry 4.0, automation, AI, IoT, and data analytics are driving innovation in manufacturing and the industry at large at a rapid pace. While these technologies promise efficiency and advancement, they also present a significant challenge: workforce readiness.
Workforce readiness is not just a requirement for the material handlers and forklift operators of the plant; it’s necessary all the way from the frontline employee to the senior executive decisionmaker.
Each of us has a role to play in a knowledge economy and a production industry augmented by advanced technology. Ultimately, our willingness and readiness to adapt will determine our ability to seize this moment.
For Learning & Development (L&D) leaders, this shift means rethinking training strategies to ensure employees can adapt to smart factories, digital workflows, and new production techniques. Traditional training methods—manuals, classroom sessions, and job-shadowing—are no longer sufficient to meet the speed and complexity of today’s industrial environments.
This guide outlines how L&D leaders can bridge the skills gap and future-proof their workforce in the era of Industry 4.0.
Understand the Industry 4.0 skills gap
The manufacturing workforce is aging, and as seasoned experts retire, they take decades of knowledge with them. At the same time, new hires often lack the digital and technical skills required to operate advanced machinery. According to a Deloitte report, the skills gap could leave 2.1 million manufacturing jobs unfilled by 2030.
To stay competitive, companies must focus on upskilling and reskilling workers at all levels—from frontline operators to engineers. The key skills needed in Industry 4.0 include:
- Digital literacy (working with AI-driven machines, IoT sensors, and cloud platforms
- Advanced problem-solving (interpreting data to optimize production)
- Collaboration in hybrid environments (humans working alongside automation and robotics)
Without the right training strategy, companies risk decreased productivity, higher turnover, and safety concerns.
What role should L&D leaders play to combat the skills gap?
L&D leaders play a critical role in closing the manufacturing skills gap by ensuring workers have the right skills at the right time. Traditional training methods are too slow for today’s evolving industry. Shifting to video-based, AI-powered, and on-demand learning enables skilled workforces and frontlines to upskill faster and more efficiently.
With an aging workforce, preserving expert knowledge is crucial. AI-driven knowledge capture helps document and transfer skills before they are lost. Companies like Timber Products have successfully standardized expertise with DeepHow, making it reusable across teams.
As Industry 4.0 introduces automation and digital tools, L&D must focus on upskilling and reskilling, including digital literacy, troubleshooting, and human-machine collaboration. Training must also be accessible and scalable, allowing workers to learn anytime, anywhere, in multiple languages.
L&D should align training with business goals by partnering with operations teams, using analytics to measure impact, and standardizing training across sites. Investing in AI-powered solutions ensures knowledge retention, higher productivity, and a workforce ready for the future of manufacturing.
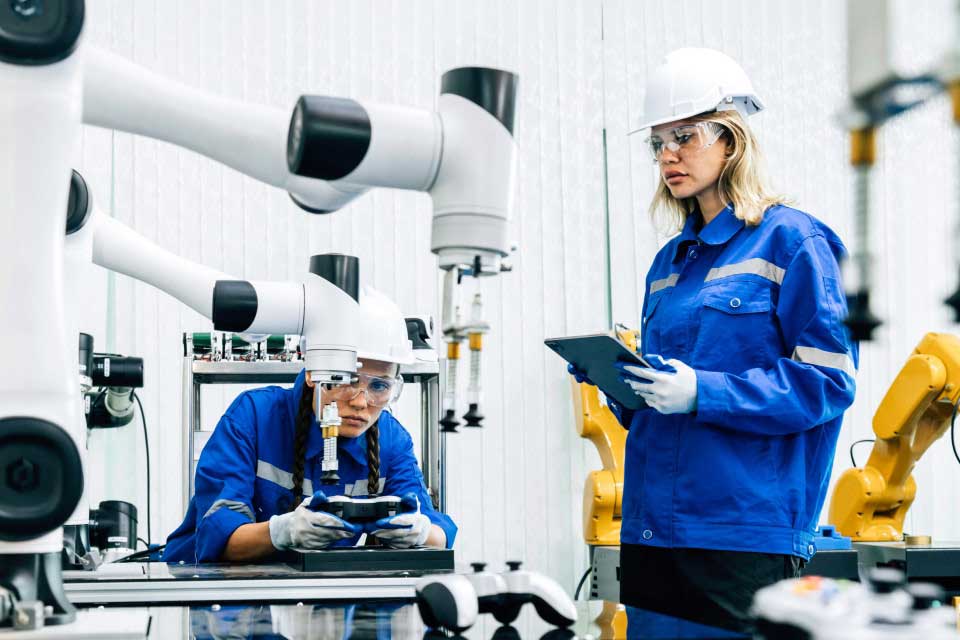
Rethink training for a digital-first workforce
L&D must evolve alongside manufacturing technology. Static PDFs, outdated PowerPoints, and lengthy classroom sessions are no longer practical. Instead, companies should adopt:
Video-centric learning
Video-based training reduces reliance on text-heavy manuals and speeds up knowledge retention. Workers can see tasks performed in real-time, making it easier to understand complex processes. DeepHow’s AI-powered video training platform helps companies create, scale, and translate expert-led training videos effortlessly. And the data backs this up: workers prefer learning through visual instructions, with 85% preferring video over text-based training.
“We reduced onboarding time by 54% and significantly cut training costs by moving to video-based learning with DeepHow.” – Stanley Black & Decker
AI-driven knowledge capture
Industry 4.0 requires agile training solutions that capture expert knowledge before it’s lost. AI-powered platforms like DeepHow can transform an experienced worker’s process into step-by-step instructional videos, ensuring that knowledge stays within the organization.
Imagine a seasoned machinist who can navigate the complexities of a CNC machine with the finesse of a virtuoso pianist, or a welder whose precision rivals that of a surgeon. These individuals aren't just ordinary workers; they're subject matter experts (SMEs).
Their wealth of experience and deep understanding of their craft make them invaluable assets in the development of training materials that resonate with learners and drive performance excellence.
Many organizational leaders grapple with the dilemma of balancing the invaluable time of skilled workers with the imperative need for comprehensive training. The traditional approach may lead them to consider engaging external consultants or relying on antiquated written standard operating procedures (SOPs). However, these routes come with their own set of challenges and drawbacks.
Engaging external consultants can be brutally expensive, and the time required to bring them up to speed on your processes can cost even more. Furthermore, despite the hefty investment, the input of seasoned workers is still required to ensure the accuracy and relevance of the training content. On the other hand, while written SOPs can still hold significant value if kept up-to-date, they often fall short of meeting the needs and preferences of today's learners.
AI makes it easy for organizations to capture expert knowledge in video without the additional requirements of hiring expensive film crews that disrupt production. With DeepHow, companies can easily capture processes with a smart phone and leverage AI to segment, transcribe, and translate expertise into bite-size training videos to train incoming employees and those looking to upskill their development.
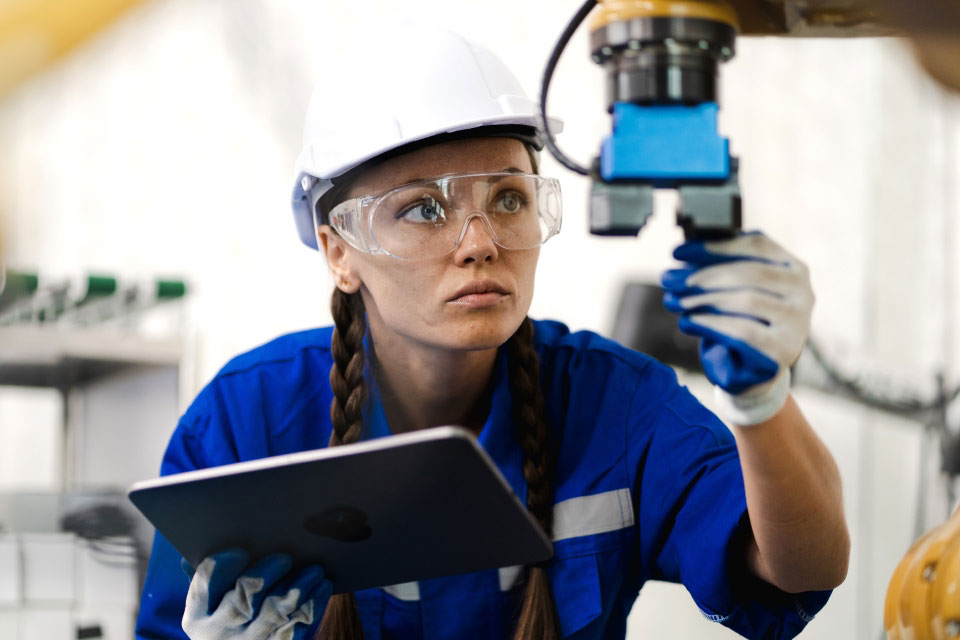
On-demand and mobile learning
With manufacturing running 24/7, workers need training that fits their schedules. Mobile-friendly, on-demand training modules allow employees to access critical information exactly when they need it, reducing downtime and increasing efficiency. For one Anheuser-Busch trainer, this was the difference between working 70 - 80 hour work weeks and being a present dad for his kids.
DeepHow offers a secure, centralized, and easily accessible library of institutional knowledge in the form of organized, searchable video content. This cuts down on the time spent searching for information and ensures that critical data is never lost. DeepHow also bypasses the limitations of traditional methods by leveraging AI technology to provide an interactive, engaging, and efficient learning experience by streamlining video creation.
Multilingual and scalable training
Global operations require training materials in multiple languages. AI-powered platforms can automatically translate technical training content, ensuring consistency across regions. As L&D leaders, prioritizing accessibility of knowledge and training for all frontline employees - regardless of their preferred language - is critical for ensuring each worker has equal access to advancement opportunities within industry 4.0.
Align training with business goals
L&D should not operate in isolation—it must directly support operational efficiency, quality, and safety. Companies should:
- Collaborate with operations teams to identify critical skill gaps
- Use training data and analytics to measure impact
- Standardize training across sites to ensure best practices are consistently applied
By aligning L&D with Industry 4.0 initiatives, manufacturers can boost productivity, reduce errors, and improve worker retention.
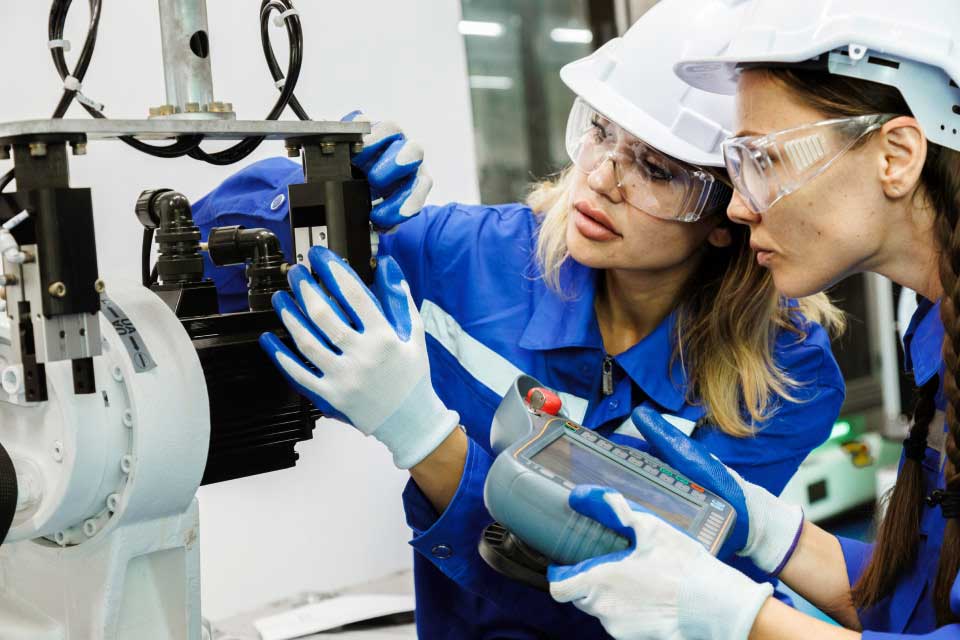
Future-proof your workforce with AI-powered training
Industry 4.0 is not just about technology—it’s about people. Investing in modern, scalable training solutions will help manufacturers build a skilled, adaptable workforce ready to thrive in a digital-first world.
L&D leaders who embrace AI-powered video training will gain a competitive edge, ensuring their teams can confidently operate in smart factories.
Are you ready to transform your workforce training? Learn how DeepHow can help you accelerate skills development with AI-powered video learning. Sign up for our mailing list to stay in touch and get the latest news on industry 4.0 for manufacturing.