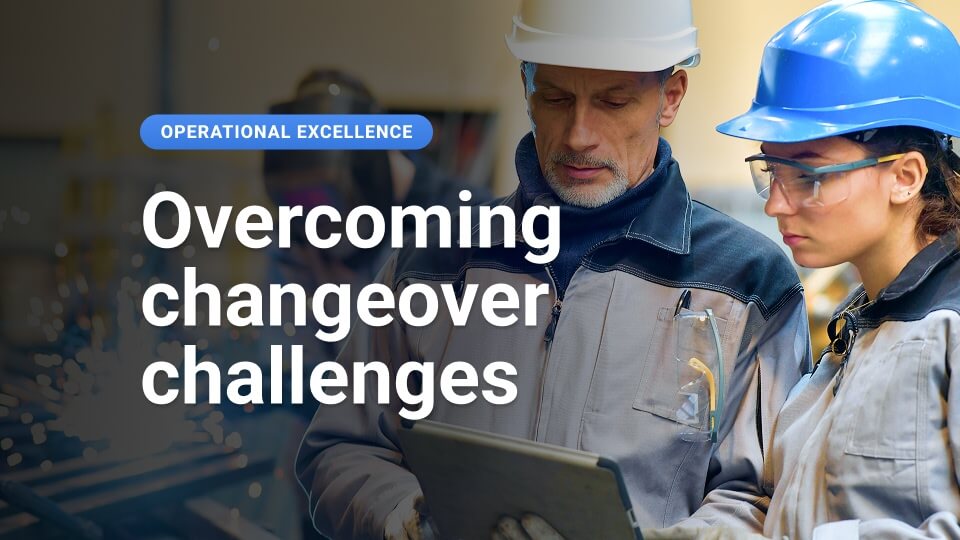
Let’s face it, changeovers are a double-edged sword. While they enable flexibility and responsiveness to market demands, they also pose significant operational challenges to execute flawlessly. From prolonged downtime to safety risks, inefficient changeovers can derail production schedules and inflate costs. However, with the right strategies and tools—like video SOPs—these challenges can be effectively addressed.
Here’s a look at the top five changeover challenges manufacturers face and actionable solutions to overcome them.
1. Prolonged Downtime
The Challenge: Lengthy changeovers disrupt production schedules, leading to missed deadlines and reduced throughput.
Solution:
- Implement video SOPs that provide step-by-step guidance, reducing guesswork and ensuring operators follow the correct procedures.
- Train workers to identify bottlenecks using data analytics to pinpoint stages that take the longest.
- Create a changeover “task force” that evaluates and improves the process over time.
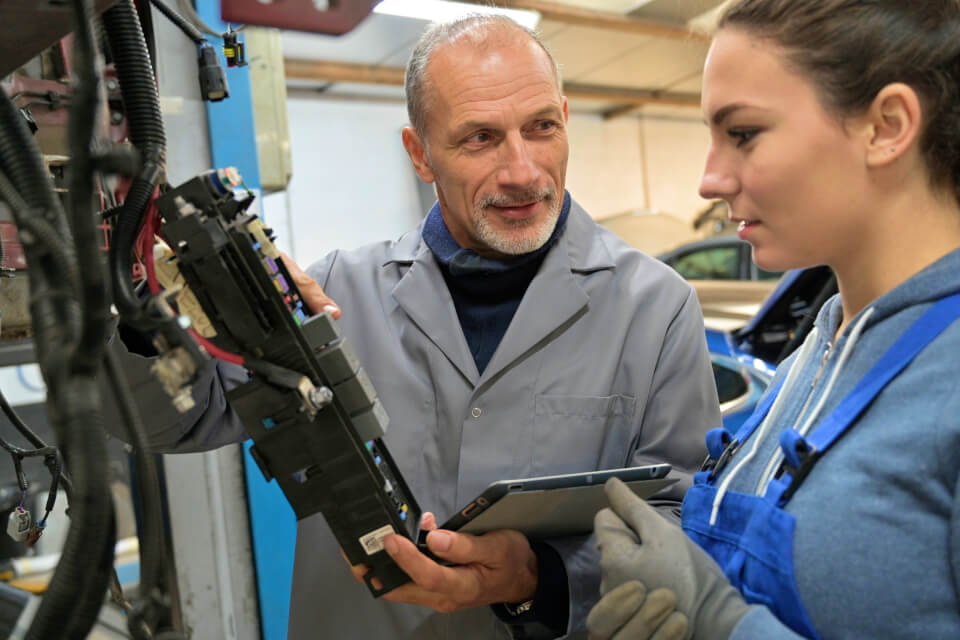
2. Lack of Standardization
The Challenge: Variability in how changeovers are performed across shifts or sites leads to inconsistent results and inefficiencies, posing risks to safety, scrap, and downtime. Even a fraction of a millimeter off can result in production scrap.
Solution:
- Use AI-powered tools like DeepHow to document best practices and distribute them across teams.
- Employ visual and interactive SOPs to ensure that every worker has access to the same high-quality training materials.
- Regularly audit procedures and provide refresher training based on video insights.
Key Tip: Multimodal SOPs can ensure consistency across global facilities, bridging communication gaps.
3. Loss of Tribal Knowledge
The Challenge: Retiring workers take decades of experience with them, leaving newer employees without critical expertise. There are an estimated 12 million manufacturing frontline workers over the age of 55 in the US alone.
Solution:
- Capture the knowledge of senior operators with video SOPs before they retire.
- Use tools like DeepHow to create a searchable library of video SOPs that document intricate steps and decision-making processes.
- Encourage a culture of knowledge sharing by incentivizing experienced workers to contribute to the training library.
Impact: Preserving this knowledge reduces dependency on individual employees and ensures long-term operational resilience.
Anhueser-Busch reduced the time to onboard each new hire by 80% after implementing DeepHow, and immediately recognized the benefits to their most tenured experts. “A maintenance team member shared that he used to conduct multiple training sessions across four teams to transfer information. Now, with DeepHow, he records the task once, and team members can review it anytime as a refresher.” - Derek Shores, Business Process Owner, Anhueser-Busch
Learn how to identify in-house experts to create the digital work instructions your team needs to succeed.
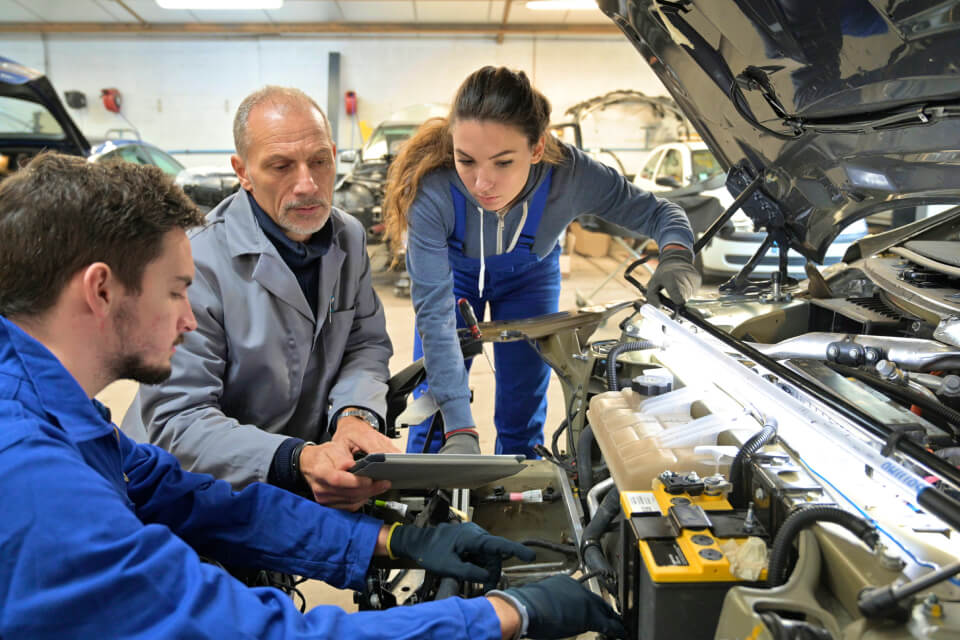
4. Complexity of Modern Equipment
The Challenge: Advanced machinery often requires specialized knowledge, increasing the likelihood of errors during changeovers. Even after conducting a changeover, experts might be needed when machines are experiencing an error or downtime, requiring supervisor-level troubleshooting before the line can begin operating again.
Solution:
- Integrate real-time video SOPs directly onto equipment interfaces using QR codes that quickly link a frontline worker with the information they need.
- Combine video SOPs with expert-led, AI-powered Q&A to provide interactive, on-the-spot guidance.
- Collaborate with equipment manufacturers to create tailored video content for complex setups that can live in an always-on knowledge library accessible to the entire frontline.
5. Safety Risks
The Challenge: High-pressure situations during changeovers can lead to oversight, resulting in accidents or non-compliance with safety protocols. Each safety incident can result in high unexpected costs for manufacturing companies.
Solution:
- Develop safety-specific video SOPs that emphasize critical steps, such as lockout/tagout procedures.
- Use videos to highlight common mistakes and safety hazards during changeovers.
- Regularly update and review training content to align with evolving safety standards.
Key Insight: Safety-focused video SOPs can also serve as compliance documentation during audits, reducing legal risks.
Learn how Timber Products effectively leveraged video SOPs to drive safety compliance, particularly in lock out / tag out processes.
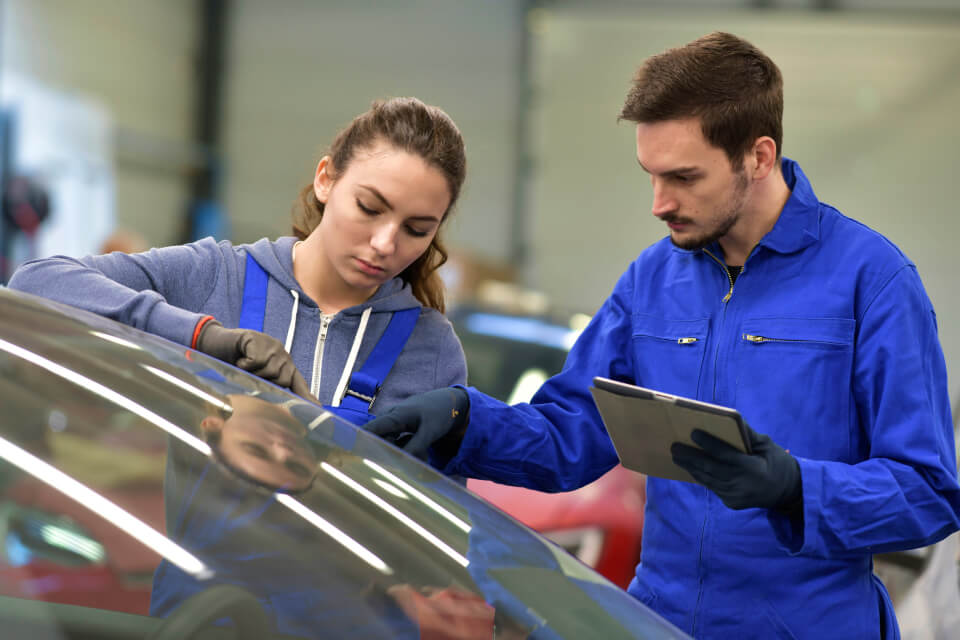
The Role of AI-Powered Video SOPs in Changeover Success
AI-powered tools like DeepHow are revolutionizing changeovers by:
- Standardizing Training: Ensuring consistent processes across shifts and sites.
- Accelerating Learning: Cutting onboarding time for new operators by up to 80%.
- Boosting Efficiency: Helping operators execute changeovers faster and with fewer errors.
- Improving Safety: Reinforcing critical safety protocols with engaging, repeatable video content.
Optimizing changeovers is essential for staying competitive in today’s fast-paced manufacturing landscape. By addressing common challenges with video SOPs and AI-driven tools, manufacturers can turn changeovers into a strength rather than a weakness.
Investing in solutions like DeepHow not only reduces downtime and errors but also empowers your workforce to execute with confidence and consistency.