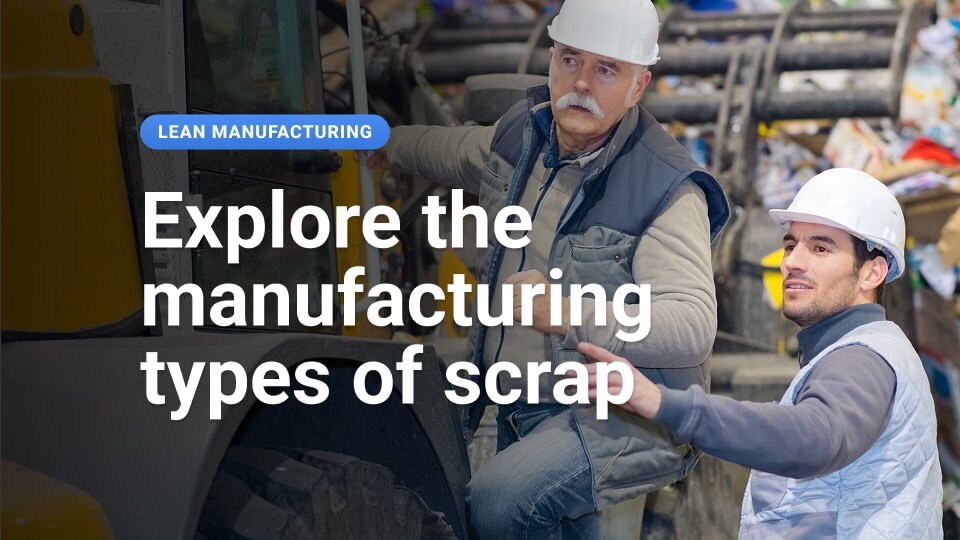
The financial and operational costs of scrap waste in manufacturing are substantial. In 2018, the United States generated approximately 292.4 million tons of municipal solid waste, with a significant portion originating from manufacturing processes. Managing this waste incurs billions of dollars in disposal fees and represents a loss of valuable materials that could have been repurposed.
The time and labor dedicated to sorting and disposing of scrap divert resources from productive activities, leading to inefficiencies.
Every frontline worker plays a pivotal role in shaping the fate of scrap materials. Whether it's identifying reusable offcuts, properly sorting waste, or adhering to efficient production techniques, the actions of each team member directly impact the amount of material wasted.
Education on scrap—knowing what can be recycled, what is truly waste, and how to minimize scrap generation—is not just a top-down initiative; it must be a shared responsibility embedded in every step of the production process. By empowering workers with knowledge, manufacturers can not only reduce costs but also move closer to their sustainability goals.
Scrap is an inevitable part of manufacturing, but its proper management is critical to reducing waste and improving efficiency. To tackle scrap effectively, it’s essential to understand its different forms, what can be reused, and what ends up as true waste.
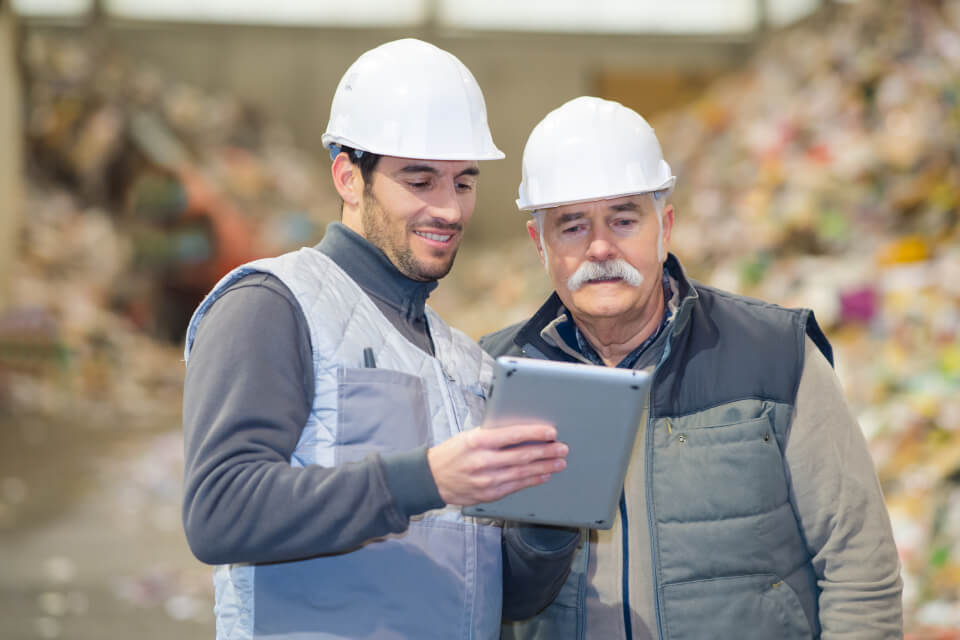
What Is Scrap in Manufacturing?
In manufacturing, "scrap" refers to leftover materials generated during production processes. These materials can come from machining, assembly, or product end-of-life. While some of it can be recycled or reused, other portions are destined for disposal. Managing scrap isn’t just about cost—it’s about sustainability, resource efficiency, and environmental responsibility.
Types of Scrap in Manufacturing: A Frontline Perspective
Effectively managing scrap begins with understanding its types and their potential for reuse. This knowledge is not just for management—it is critical for the frontline workforce, who directly handle materials and influence scrap outcomes during production. By equipping frontline workers with the ability to identify, sort, and manage scrap effectively, manufacturers can reduce waste, lower costs, and enhance sustainability. Here's a closer look at the types of scrap commonly encountered in manufacturing:
1. Prompt Scrap: Materials generated directly from production processes, such as offcuts, trimmings, or defective parts.
- Example: Steel shavings from machining or plastic cuttings from an injection mold.
- Reusability: High. These materials are often recyclable or reusable when sorted correctly.
- Why Frontline Matters: Workers on the line can quickly identify and segregate prompt scrap for recycling, ensuring valuable materials are recovered rather than wasted.
2. Obsolete Scrap: Scrap from end-of-life products like decommissioned machinery, vehicles, or appliances.
- Example: An outdated assembly line machine or a broken electronic device.
- Reusability: Moderate. Components and raw materials can often be salvaged but may require specialized recycling processes.
- Why Frontline Matters: Frontline teams can assist in disassembling obsolete equipment, recovering usable parts, and reducing the volume of true waste.
3. Contaminated Scrap: Materials mixed with hazardous substances or chemicals, making them difficult or unsafe to recycle.
- Example: Oil-soaked metal parts or adhesive-laden plastics.
- Reusability: Limited without advanced treatment methods.
- Why Frontline Matters: Training workers to handle contaminated materials safely and segregate them correctly prevents cross-contamination, protecting both recycling streams and the environment.
4. Composite Material Scrap: Products made of mixed materials that are challenging to separate, such as multi-layered packaging or fiber-reinforced plastics.
- Example: Plastic bonded to metal or laminate materials.
- Reusability: Rare. Separation processes are often too costly or impractical.
- Why Frontline Matters: Educated workers can flag composite scrap early, ensuring it is managed appropriately and not mixed with recyclable materials.
5. Degraded Scrap: Materials that have lost structural integrity or quality after multiple cycles of use or recycling.
- Example: Plastics that have become brittle or metals with impurities.
- Reusability: Minimal to none.
- Why Frontline Matters: Frontline workers are often the first to notice degradation in materials and can report or isolate these scraps, ensuring they don’t compromise production or recycling efforts.
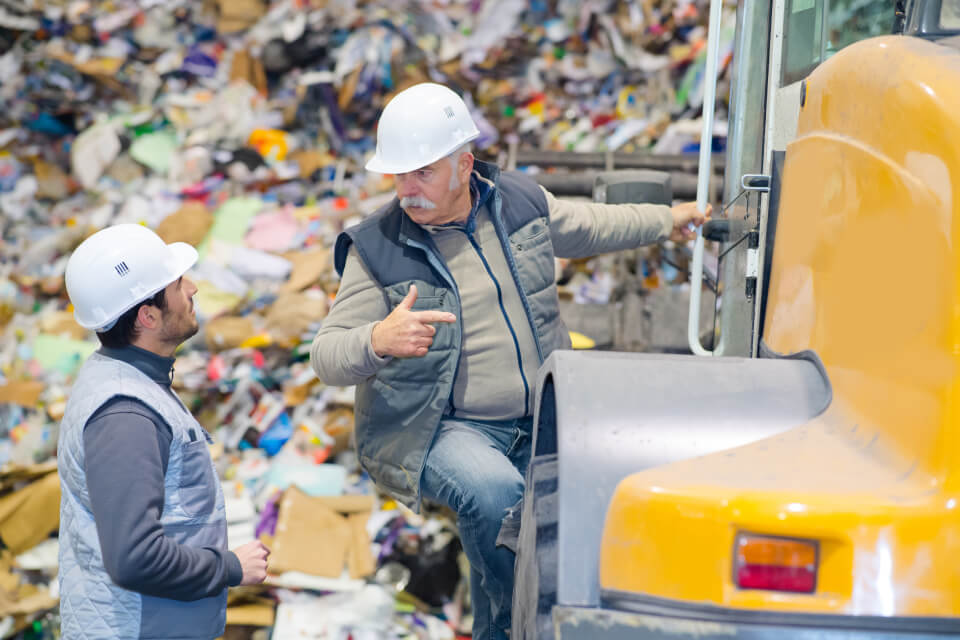
Reusable Scrap vs. True Waste Scrap
Effectively managing scrap in manufacturing starts with a clear understanding of what is reusable versus what constitutes true waste. This distinction not only helps manufacturers reduce their environmental footprint but also enhances resource efficiency, cost savings, and overall sustainability. At the heart of this effort lies the frontline workforce, whose hands-on involvement is critical to identifying and handling scrap correctly.
Reusable Scrap
Reusable scrap includes materials that retain value and can be reintegrated into production or recycled for new applications. These materials are the key to reducing waste and maximizing efficiency:
- Metals like aluminum and steel: These highly recyclable materials can be melted down and repurposed repeatedly without significant loss of quality.
- Certain plastics: Durable plastics that maintain structural integrity after recycling can be processed into new products, reducing dependency on virgin materials.
- Excess production material: Surplus materials such as trimmings or offcuts can often be directly reused within the manufacturing process, saving resources and costs.
Educating frontline workers to recognize reusable materials ensures these valuable resources are properly identified and redirected back into the production process or recycling stream.
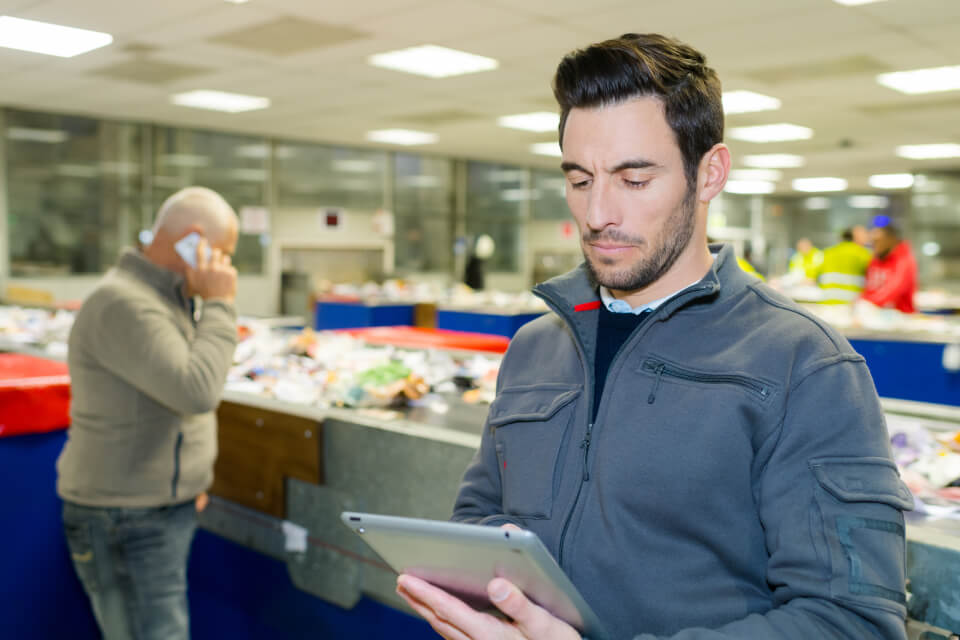
True Waste Scrap
True waste scrap represents materials that are either impractical or too costly to reuse or recycle. These pose significant challenges for waste management:
- Contaminated materials: Items tainted with hazardous chemicals or residues require complex treatments that are often uneconomical or environmentally unfriendly.
- Mixed composites: Products made of multiple materials bonded together (e.g., plastic-metal composites) are difficult and expensive to separate for recycling.
- Low-value materials: Certain plastics or byproducts lack viable recycling markets, making recovery cost-prohibitive.
Training frontline workers to properly identify true waste and manage it responsibly helps minimize environmental impact and prevent contamination of recyclable streams.
The Role of the Frontline in Scrap Management
The distinction between reusable and true waste scrap is not only a technical challenge but also a frontline responsibility. Workers on the factory floor have a unique vantage point—they see scrap being generated in real-time and are instrumental in its sorting and handling.
By empowering frontline employees with the knowledge to differentiate between reusable and waste scrap, manufacturers can:
- Increase resource recovery: Maximizing the reuse of materials saves costs and reduces reliance on virgin resources.
- Reduce waste disposal needs: Proper sorting ensures that true waste is minimized, and reusable materials are not mistakenly discarded.
- Enhance sustainability goals: A well-informed workforce actively contributes to reducing the environmental footprint of the manufacturing process.
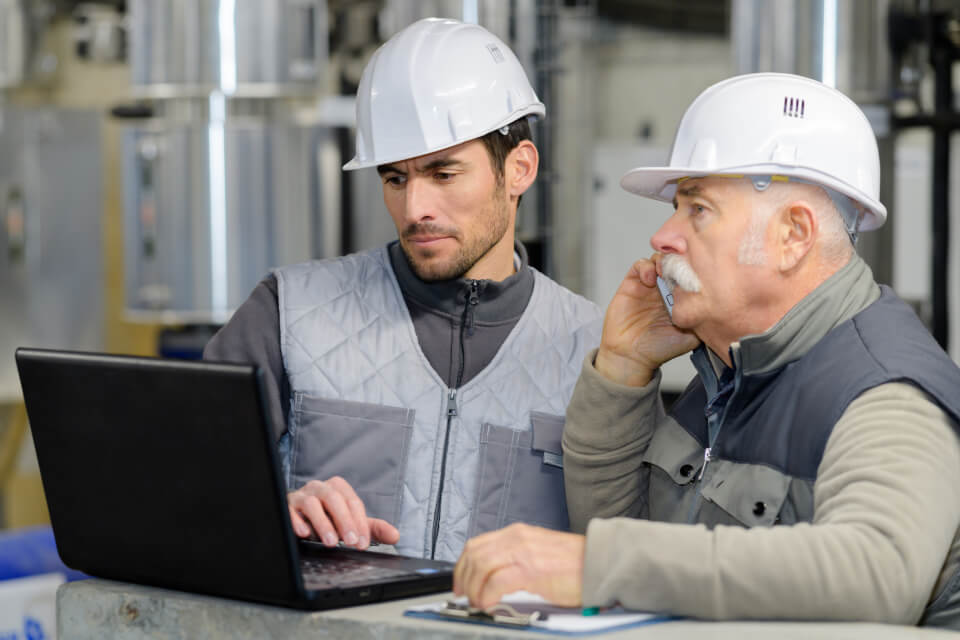
Reducing Scrap Through Frontline Empowerment
Effective scrap management begins on the factory floor, where decisions and actions in real-time can significantly impact waste levels. This is where DeepHow plays a critical role. By leveraging an AI-powered video companion while they work, DeepHow ensures frontline workers are equipped with the expertise to minimize errors, optimize material use, and identify opportunities for reducing scrap at every step of the process.
Whether it's through capturing tribal knowledge, standardizing procedures, or enhancing team collaboration, DeepHow empowers workers to execute tasks with precision and confidence. This translates to fewer production errors, better material utilization, and less waste overall.
Moreover, DeepHow’s multimodal Standard Operating Procedures (SOPs) provide clear, actionable guidance tailored to specific roles and scenarios and in a variety of formats to meet a range of learning needs. By bridging knowledge gaps and fostering a culture of continuous improvement, DeepHow helps manufacturers move closer to achieving their zero-waste goals.
Apply Your Knowledge & Equip Your Frontline
Scrap in manufacturing, whether reusable or waste, represents both a challenge and an opportunity. By understanding its types, origins, and impact, manufacturers can implement targeted strategies to reduce waste and optimize processes. The key lies in empowering the workforce with the tools and training needed to make informed decisions at every stage of production.
DeepHow’s innovative approach to frontline training and knowledge management positions manufacturers to not only reduce scrap but also improve operational excellence and sustainability. Together, we can turn scrap management from a cost center into a cornerstone of a greener, more efficient future.
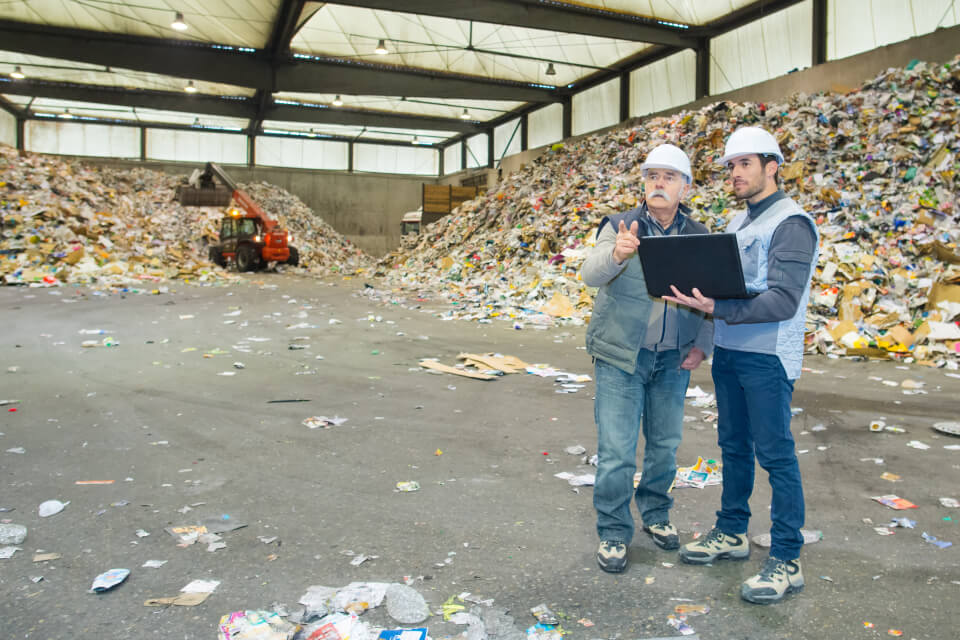