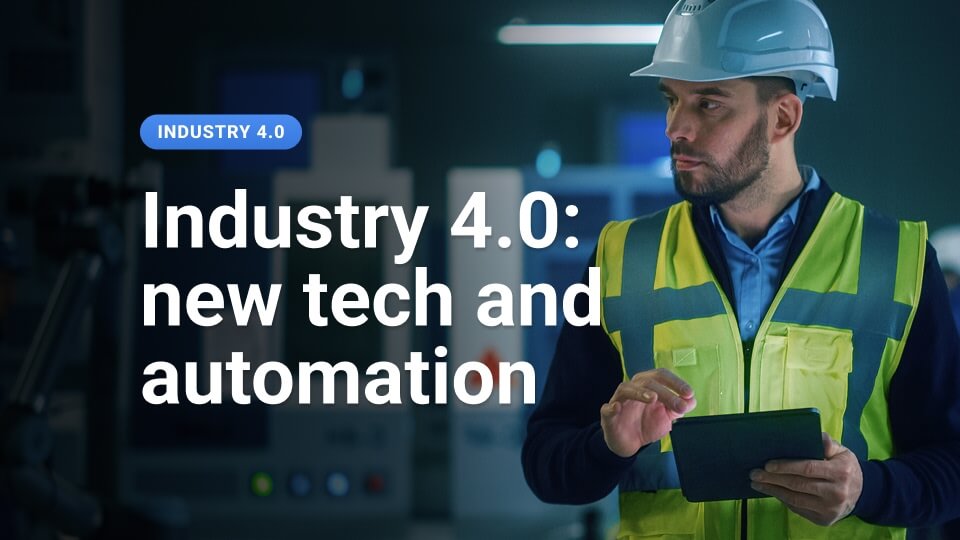
Industry 4.0 is both disrupting and transforming manufacturing with the integration of advanced technologies, AI, and automation. For operations leaders, preparing the workforce to embrace this shift is pivotal to achieving operational excellence and sustaining growth. This adaptation extends beyond simply acquiring new tools—it involves fostering a culture of continuous learning, addressing skill gaps, and strategically upskilling employees to thrive in this new landscape.
Why Workforce Preparation is Crucial
The looming skills shortage poses a significant threat, with the U.S. manufacturing sector potentially facing 2.1 million unfilled positions by 2030. Additionally, 69% of manufacturing companies report challenges due to skill deficits. These gaps are exacerbated by the accelerated retirement of seasoned workers, risking the loss of invaluable institutional knowledge. Investing in upskilling and training is not just beneficial—it’s essential for future-proofing operations.
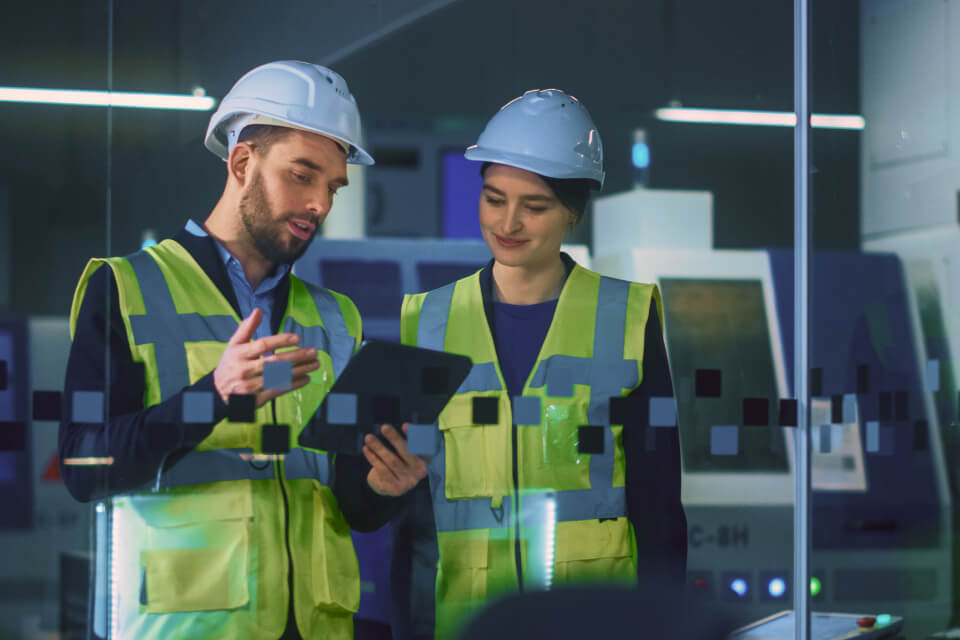
Embracing Advanced Learning Solutions
Modern training strategies leverage AI, video-based instruction, and multimodal SOPs to cater to diverse learning preferences. Research indicates that younger workers, who will comprise 64% of the workforce by 2031, favor visual training methods; 85% prefer video over traditional text manuals. This preference highlights the importance of integrating visual and interactive learning to maintain engagement and boost knowledge retention. DeepHow’s AI-powered video training exemplifies how technology can simplify complex processes, ensuring information is clear and easily accessible.
Key Approaches to Effective Training:
- Visual and Multimodal SOPs: Implement SOPs that use videos, audio, and text to provide employees with detailed, intuitive instructions. This combination aids understanding, supports cross-generational training, and ensures consistency across operations.
- Continuous Upskilling Programs: Create ongoing learning initiatives that align with evolving technology. Regularly update training materials to keep them relevant, fostering a culture of adaptation.
- AI Integration for Training: Utilize AI-powered tools to automate and enhance training processes. AI can help personalize learning experiences, making training more efficient and impactful.
Real Benefits of Adapting Training Approaches
Adaptation isn’t just an investment; it yields measurable returns. Companies that have prioritized digital training tools report up to a 30% increase in operational efficiency. Furthermore, strong onboarding and training programs are shown to increase employee retention by up to 82%. For operations leaders, this means not only retaining top talent but also creating a workforce that’s equipped to handle complex technological tasks, thereby reducing downtime and maintaining productivity.
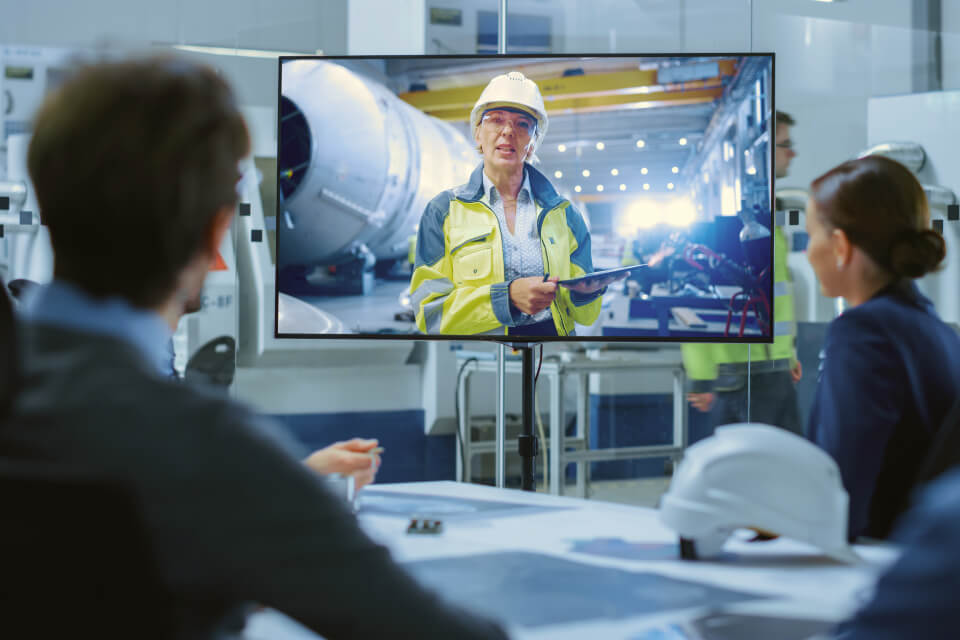
The Importance of Knowledge Transfer
As baby boomers retire, manufacturers face the risk of losing 'tribal knowledge', or legacy knowledge—critical, experience-based insights that are difficult to document. To combat this, companies need effective knowledge transfer systems. Solutions like video SOPs enable experienced workers to record their expertise, which can be referenced by newer employees, ensuring continuity and operational consistency.
Barriers to Adoption and How to Overcome Them
Despite the clear benefits, challenges persist in integrating new training technologies. These include resistance to change and budget constraints, with 39% of organizations citing insufficient resources as a hindrance to adopting effective training programs. To overcome these barriers, leaders should:
- Champion the Change: Demonstrate the value of new training tools through pilot projects that showcase tangible results.
- Assign Dedicated Headcount: Allocate trainers and support staff to champion the rollout and continuous improvement of training programs.
- Engage Employees Early: Include the workforce in the adoption process, soliciting feedback and refining approaches based on their needs.
- Allocate Budgets Strategically: Shift funds towards training initiatives that align with long-term business goals, focusing on solutions proven to enhance productivity and engagement.
- Align to KPIs for Accelerated Impact: Explicitly include Industry 4.0 goals in organization-wide key performance indicators to ensure that mid-level managers are equally committed to improving technology skill development.
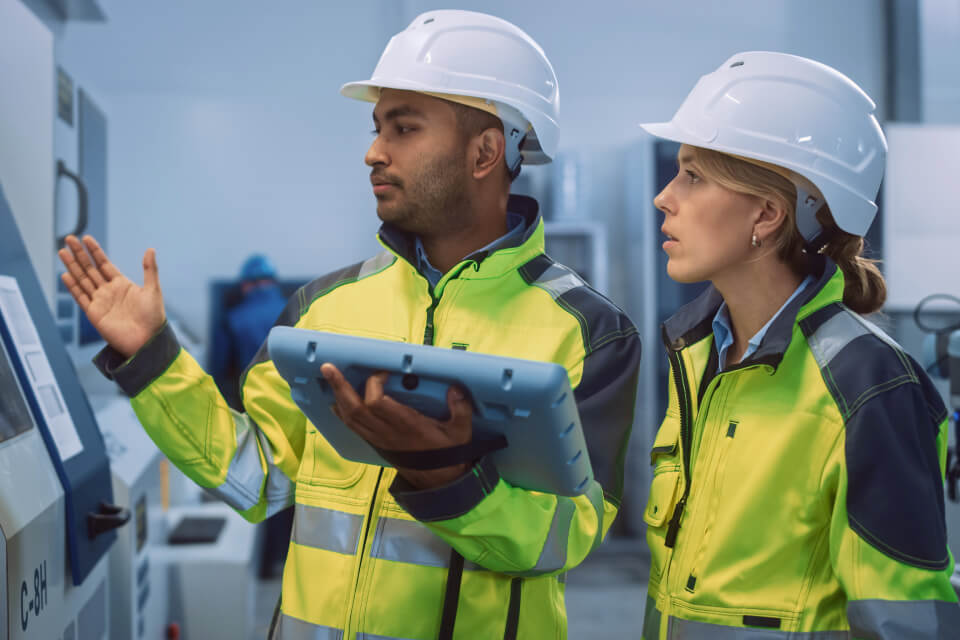
Building a Culture of Continuous Improvement
Creating a learning culture extends beyond training for new technology. It involves fostering an environment where employees feel supported and are encouraged to develop new skills. This not only increases engagement—where 92% of employees report positive effects from well-structured training programs—but also leads to long-term retention and loyalty.
The path to adapting to new technology and automation in manufacturing involves strategic investment in training and workforce development. By leveraging multimodal SOPs, video training, and AI-driven tools, operations leaders can bridge skill gaps, retain crucial knowledge, and cultivate a workforce ready for Industry 4.0. Preparing today ensures resilience and competitiveness for tomorrow.