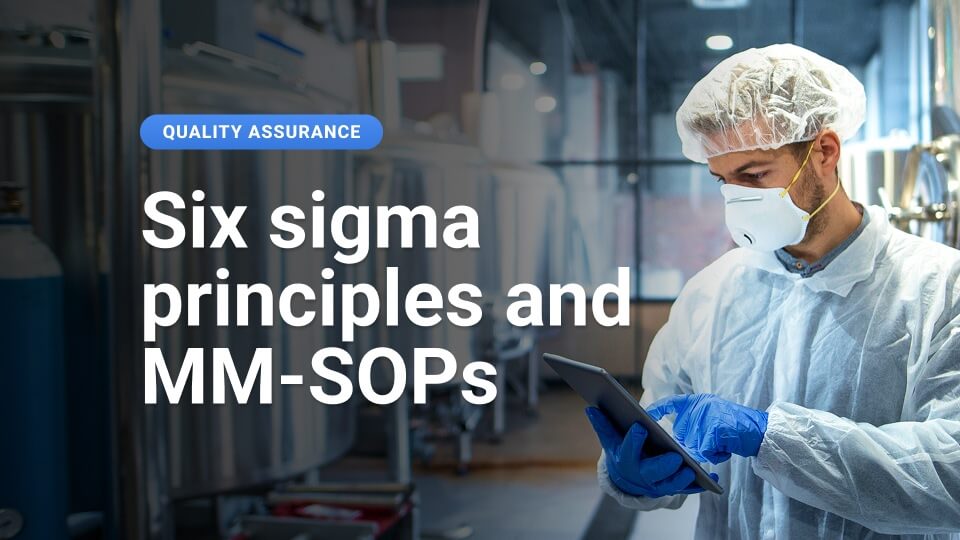
In 1986, a wave of innovation and progress swept across various fields. It was the year that saw the introduction of the world's first disposable camera, the launch of Pixar Animation Studios with its groundbreaking short film Luxo Jr., and the debut of the iconic video game series The Legend of Zelda. In the industrial world, 1986 also brought about the creation of the groundbreaking Six Sigma quality improvement methodology. Developed by engineers at Motorola, Six Sigma was designed to enhance manufacturing processes by identifying and eliminating defects, ultimately setting new standards for efficiency and excellence in production. This innovative approach soon became a cornerstone for continuous improvement in countless industries.
Today, artificial intelligence (AI) is taking Six Sigma and the lean process to new heights by significantly enhancing data analysis, process efficiency, and defect detection. With AI-driven tools like DeepHow Maven and AI Quizzing, organizations can swiftly analyze vast amounts of data, uncovering insights and patterns that traditional methods might miss. This leads to more precise identification of root causes, streamlined processes, and predictive maintenance, ultimately driving greater efficiency and fostering quality improvement. By integrating AI into Six Sigma and lean process practices, companies can achieve process efficiency and continuous improvement at an accelerated pace, ensuring they stay competitive in an increasingly complex and fast-paced market.
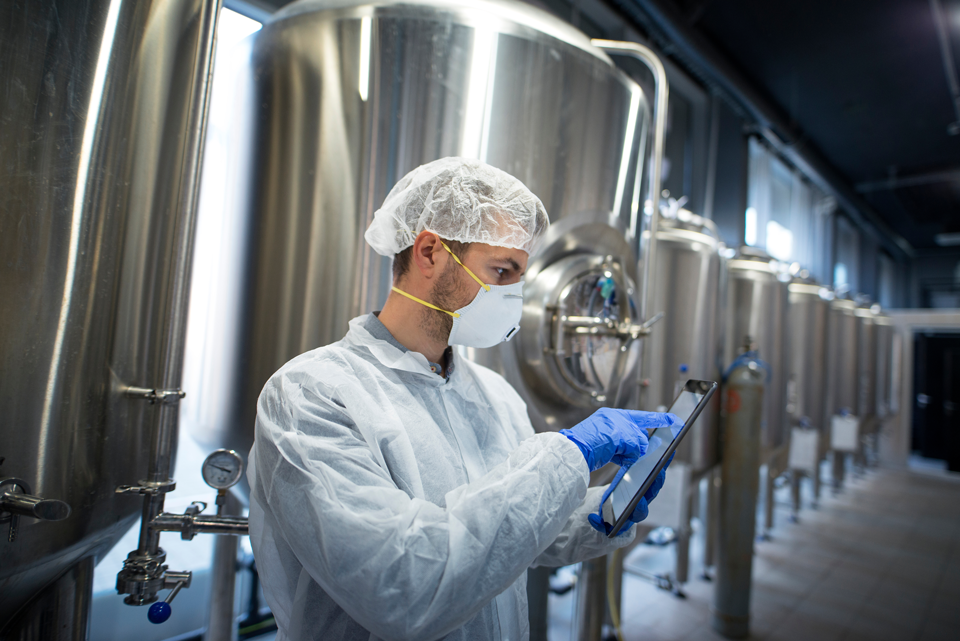
Six Sigma: A Brief Overview
Six Sigma is a data-driven methodology designed for error reduction and quality improvement in business processes, often integrated with the lean process approach. It is grounded in the DMAIC framework, which stands for Define, Measure, Analyze, Improve, and Control. Each phase of DMAIC serves a distinct purpose in identifying and eliminating defects, ensuring that processes operate at their highest potential.
- Define: Identify the problem and project goals.
- Measure: Collect data to understand current performance.
- Analyze: Investigate the data to identify root causes of defects.
- Improve: Implement solutions to address root causes and improve the process.
- Control: Monitor the improvements to ensure sustainability.
Here are several use cases for Six Sigma:
Food and Beverage Industry: For several major cola companies, Six Sigma is used to streamline bottling processes and reduce waste. It helps in maintaining consistent taste and quality across different batches, thereby enhancing customer experience and reducing costs.
Automotive Industry: In car manufacturing, Six Sigma methodologies are used to reduce defects in assembly lines, ensuring each vehicle meets stringent quality standards. For instance, one manufacturer has applied Six Sigma for error reduction in engine assembly, leading to higher reliability and customer satisfaction.

DeepHow’s AI: A Snapshot
DeepHow leverages the latest AI to create sophisticated training and process optimization tools. Two features, DeepHow Maven and AI Quizzing, exemplify how AI can be harnessed to support Six Sigma and lean process initiatives.
- DeepHow Maven: An AI-powered knowledge capture and training platform that converts video demonstrations into comprehensive, multimodal SOPst. Key offerings:
- SOP Studio: Convert video demonstrations into comprehensive Multimodal SOPs.
- Ask Maven: Ask direct questions about the knowledge you have documented, eliminating the steps of finding and searching through documents for specific information.
- Multimodal SOP Integration: Connect your Multimodal SOPs to the tools you already use. Create text SOPs and use them in your preferred tools, or integrate the full Multimodal SOPs with your LMS and LXP systems.
- AI Quizzing: An intelligent assessment tool that generates quizzes to test knowledge retention and comprehension.
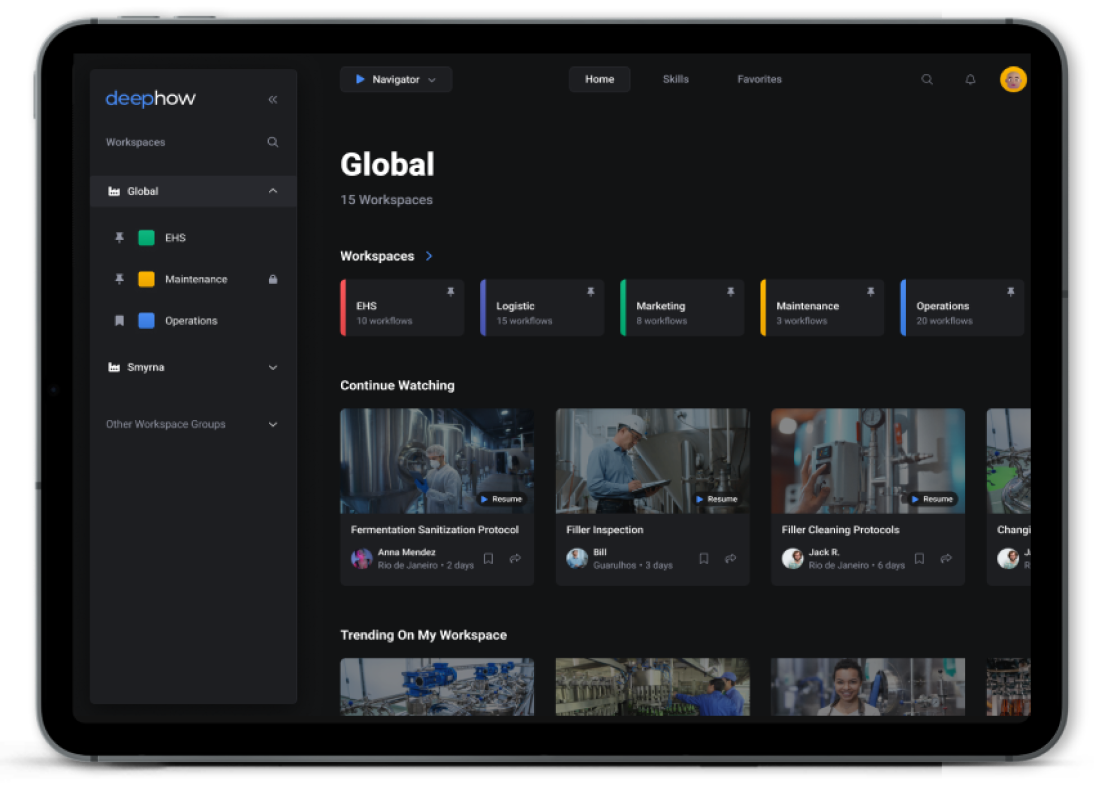
Aligning DeepHow's AI with Six Sigma Principles
DeepHow’s AI tools align with Six Sigma principles by enhancing each phase of the DMAIC process. This alignment not only contributes to error reduction but also facilitates a culture of continuous improvement.
Define
In the Define phase, the goal is to clearly articulate the problem and set objectives. DeepHow Maven plays a crucial role here by utilizing AI to convert video demonstrations into dynamic, multimodal SOPs. These SOPs serve as a reference for defining project goals and understanding the current process landscape.
For instance, when defining a problem related to equipment maintenance, DeepHow Maven can provide step-by-step multimodal SOPs and documentation created by experienced technicians. This ensures that all team members have a uniform understanding of the problem, leading to more precise problem statements and objectives.
Measure
Accurate measurement is critical in Six Sigma as it establishes a baseline for improvement. DeepHow’s AI-driven platform for creating and sharing multimodal SOPs and instructions from video demonstrations ensures that measurement procedures are standardized and easily replicable. DeepHow Maven’s comprehensive, multimodal SOPs and guides ensure that employees follow consistent methods when collecting data, which enhances the reliability of the measurements.
Moreover, AI Quizzing can be employed to assess employees’ understanding of measurement techniques. By generating quizzes that test knowledge of data collection procedures, AI Quizzing helps ensure that staff members are proficient in the necessary skills, thereby reducing variability in the measurement phase.
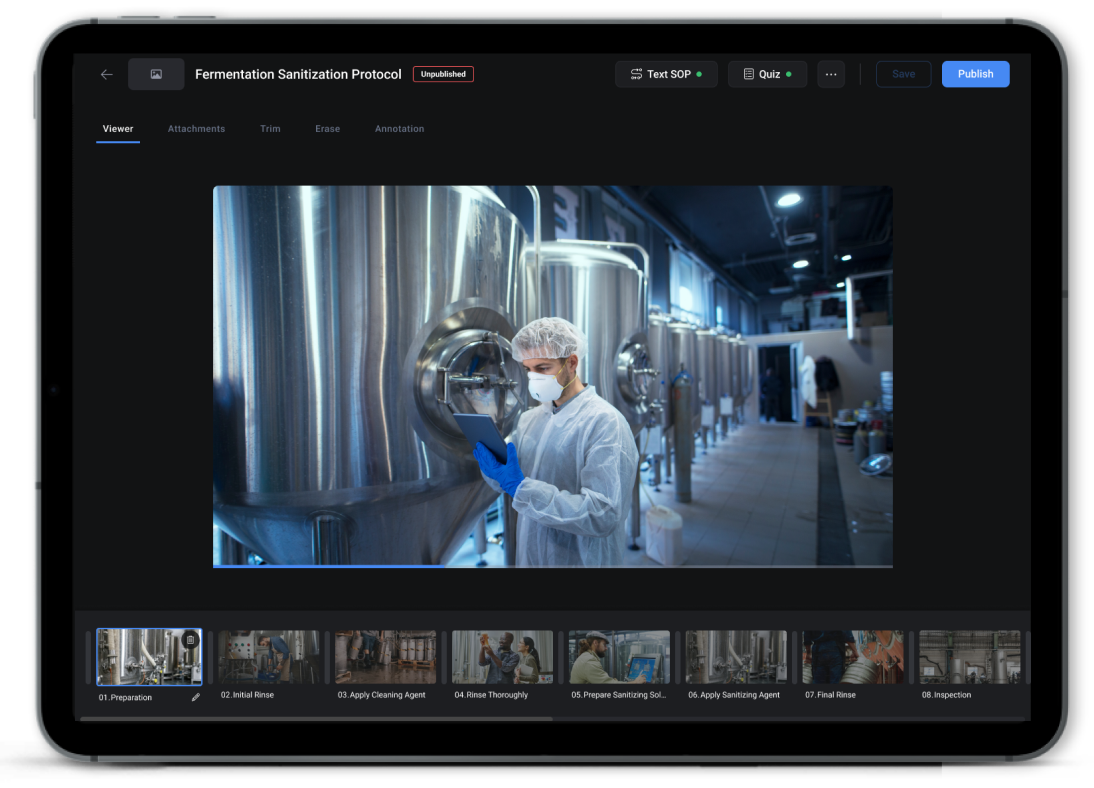
Analyze
In the Analyze phase, the focus is on identifying the root causes of defects. DeepHow’s tools facilitate this phase by providing comprehensive training on analytical techniques and tools. DeepHow Maven can create comprehensive Multimodal SOPs, including interactive videos SOPs, written/text SOPs, AI-generated summaries, and learning assessments, that breaks down complex analytical methods into easy-to-understand tutorials, making it accessible for all team members.
Furthermore, AI Quizzing can reinforce this knowledge by assessing employees’ grasp of analytical concepts and techniques. By identifying gaps in knowledge, AI Quizzing ensures that all team members are adequately prepared to participate in root cause analysis, leading to more accurate identification of defects and their causes.
Improve
The Improve phase involves implementing solutions to address the root causes of defects. DeepHow Maven is instrumental in this phase by providing detailed multimodal SOPson best practices and improvement techniques. This ensures that employees are well-equipped to implement changes correctly and effectively.
For example, if a solution involves a new assembly procedure, DeepHow Maven can create instructional content demonstrating the correct way to perform the procedure. This leads to error reduction during implementation and ensures that improvements are standardized across the workforce.
AI Quizzing supports the Improvement phase by testing employees on the new procedures and changes. By ensuring that employees have thoroughly understood and retained the new methods, AI Quizzing helps reduce the likelihood of reverting to old, inefficient practices.
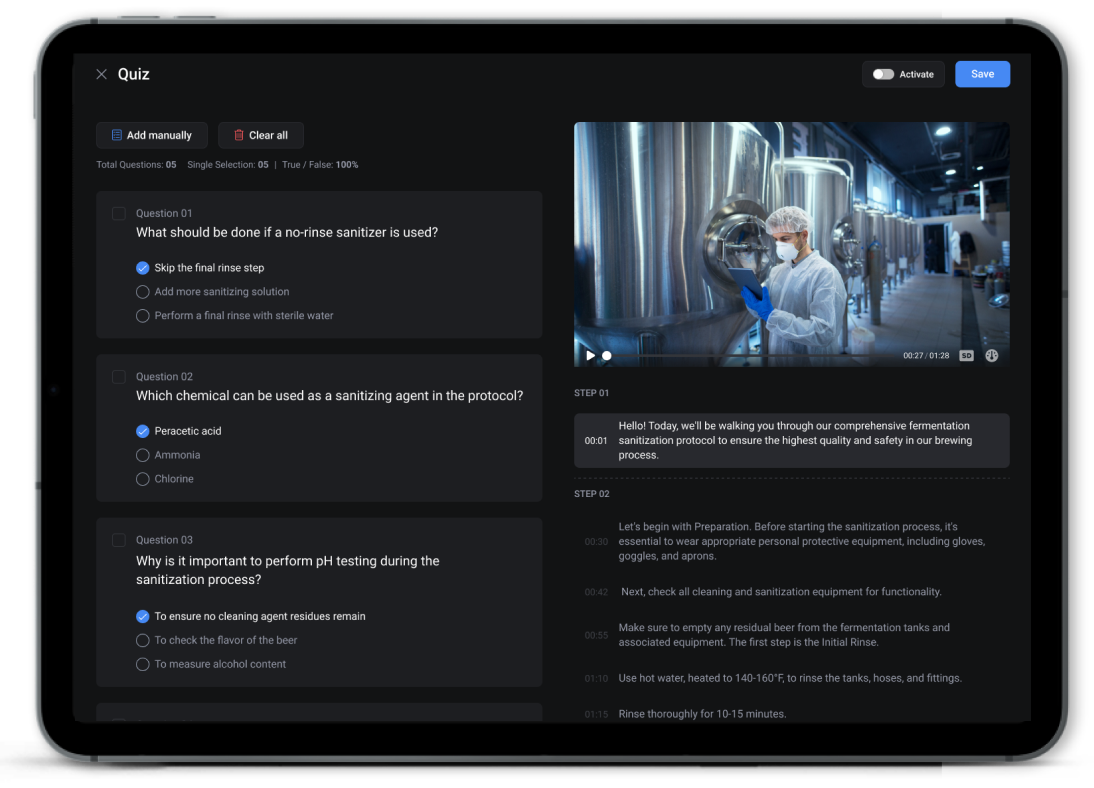
Control
The final phase of DMAIC, Control, focuses on sustaining the improvements made. DeepHow’s AI tools provide ongoing training and assessments to ensure that employees continue to adhere to the new processes. DeepHow Maven’s multimodal SOPs can be used for refresher training, ensuring that employees do not forget the new procedures over time. AI Quizzing can be used periodically to assess retention and understanding of the new processes, identifying any areas where further training may be required. By providing continuous support and assessment, DeepHow’s generative AI tools help maintain the gains achieved during the improvement phase, ensuring long-term process efficiency and stability.
Fostering a Culture of Continuous Improvement
One of the key benefits of integrating DeepHow’s AI tools with Six Sigma principles and the lean process is the promotion of a culture of continuous improvement. By improving training outcomes and reducing variability in employee performance, these tools help create an environment where ongoing learning and process optimization are ingrained in the organizational culture.
- Enhanced Training Outcomes: DeepHow Maven ensures that training materials are consistently high-quality and derived from expert knowledge. This leads to more effective training programs, with employees gaining a deeper understanding of processes and techniques. AI Quizzing further reinforces this by regularly testing and refreshing employees’ knowledge, ensuring that learning is retained and applied correctly.
- Reduced Variability in Performance: Standardized training and consistent assessments reduce variability in how employees perform their tasks. This uniformity is crucial in maintaining high-quality standards and minimizing defects. By ensuring that all employees follow the same procedures and have the same level of understanding, DeepHow’s AI tools contribute to more predictable and reliable process outcomes.
- Data-Driven Decision Making: The use of AI in training and assessment provides valuable data on employee performance and knowledge retention. This data can be analyzed to identify trends and areas for improvement, enabling more informed decision-making. This aligns with the Six Sigma emphasis on data-driven approaches, ensuring that decisions are based on empirical evidence rather than intuition.
- Continuous Feedback Loop: DeepHow’s AI tools create a continuous feedback loop where employees receive regular assessments and updates on their performance. This ongoing feedback is essential for continuous improvement, as it helps identify and address issues promptly before they escalate into significant problems.
DeepHow’s latest AI features, DeepHow Maven and AI Quizzing, represent a significant advancement in aligning AI technology with Six Sigma principles and the lean process. By enhancing each phase of the DMAIC process, these tools drive process efficiency, reduce errors, and improve workforce training. Furthermore, they foster a culture of continuous improvement by ensuring that employees are consistently trained, assessed, and supported in their roles.