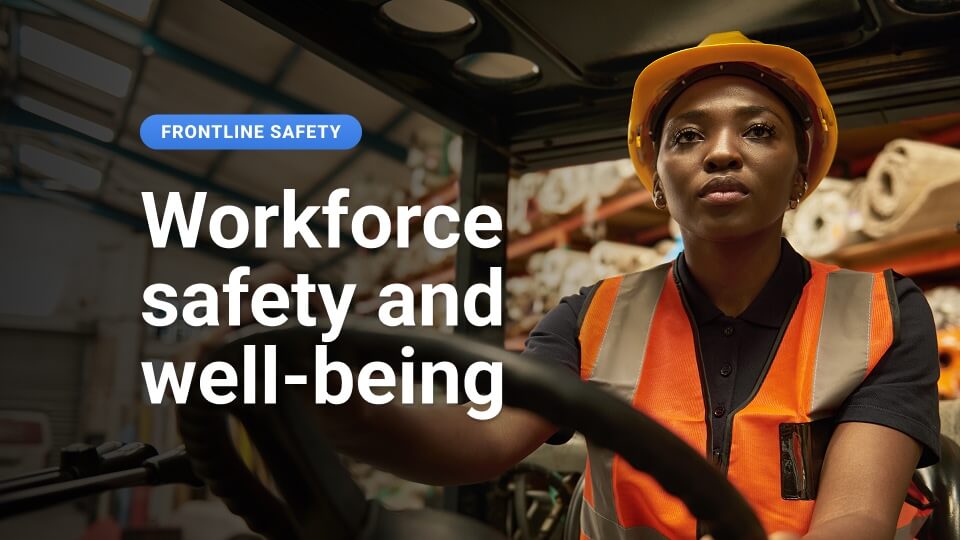
Ensuring the safety and well-being of a workforce is more than just a regulatory obligation; it's a moral responsibility. More than that, positive environmental health and safety is a pillar of employee well-being, productivity, and overall business reputation.
In recent years, technological advancements, changing labor markets, and evolving environmental considerations have overhauled the industrial landscape. Within this complexity, maintaining a culture of safety across diverse workforces, shifts, and sites is a key challenge leaders must prioritize. The actual obstacle isn't just setting up a safety culture, but it's about ensuring each employee genuinely understands, supports, and carries it forward each day.
Safety training methods of the past need to adapt to the current times. These tend to be one-size-fits-all and fail to consider each employee’s individual learning styles and needs
This can lead to critical information being lost or misunderstood, and unfortunately, these minor lapses can result in catastrophic accidents and even loss of life. The link between labor shortages and an increase in accidents and injuries has become a topic of grave concern. Recent data indicate a significant surge in these incidents. Specifically, fatalities and injuries increased from 366 per 100,000 workers in 2019 to a staggering 429 per 100,000 workers in 2021. This unsettling escalation marks an approximate 17% increase in just two years, a rate industry safety experts find alarming.
Let's reimagine employee safety training. Picture this: a workplace where safety training isn't just a mandatory tick on the checklist but an engaging, intuitive experience that employees look forward to. Where sophisticated technology blends seamlessly with training programs to enhance their effectiveness and make workplaces safer and more productive. This isn't some futuristic utopia. It's a reality made possible when employers leverage DeepHow, an AI-powered solution transforming safety training.
The Challenge of Consistent Safety Practices
Workplace safety is an undeniable priority, yet a continuous challenge. For every procedure meticulously followed, there's an unanticipated risk lurking. For every near-miss averted, a potential disaster awaits in the wings. And all the while, the goalposts are shifting as technology evolves, regulatory standards tighten, and the complexity of tasks multiplies.
One of the most poignant challenges is consistency in safety training and practices. With multiple work sites, diverse teams, and various tasks, how can one ensure that safety protocols are uniformly understood and implemented? And when these protocols change, how do you guarantee that everyone stays up-to-date?
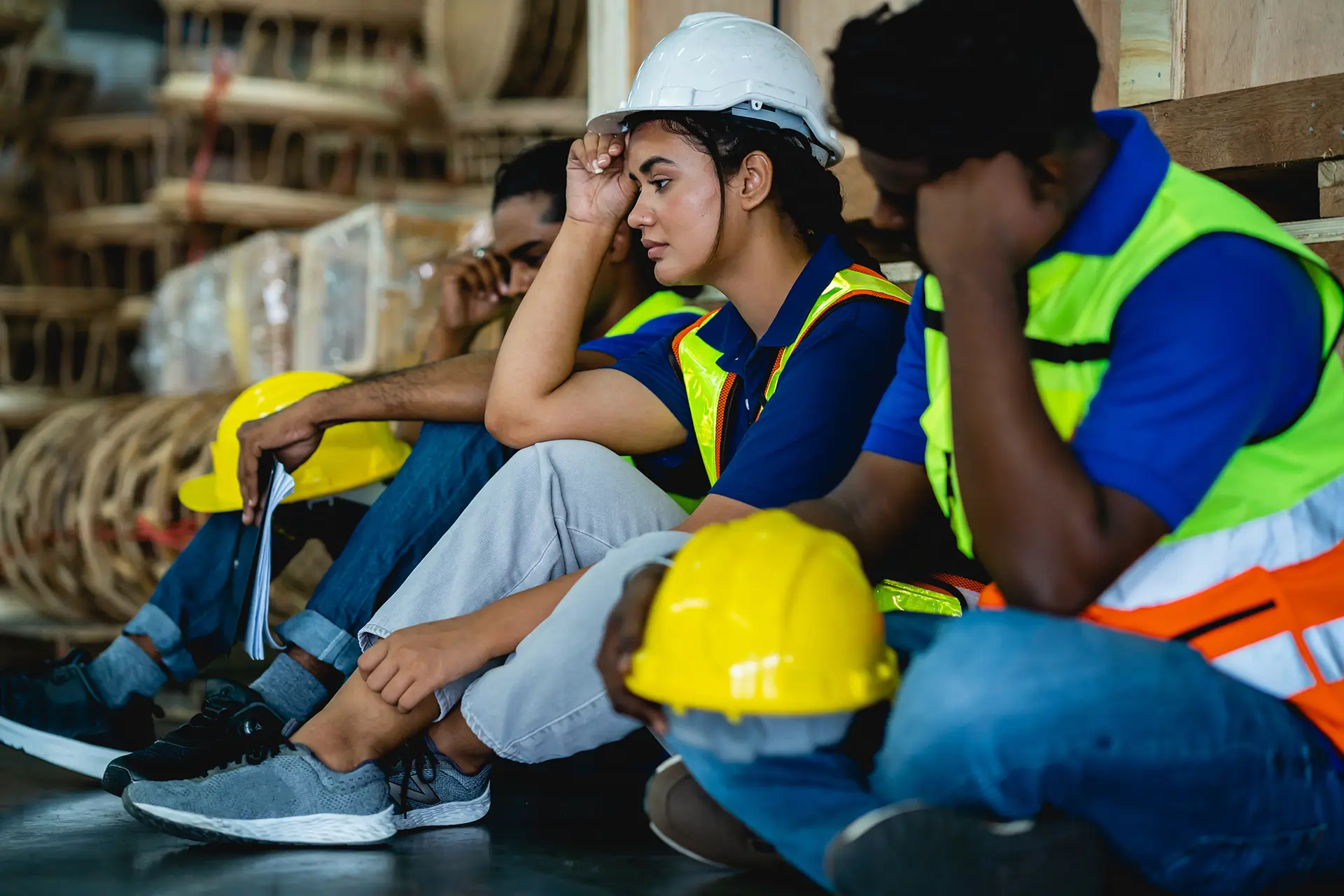
Safety Protocol Challenges
- Industry complexities: The importance of workplace safety is a given, but the practical application is complex and challenging. The evolution of technology, tightening regulatory standards, and the complexity of tasks multiply these challenges.
- Consistency: A significant hurdle is ensuring that safety protocols are uniformly understood and implemented across multiple work sites, diverse teams, and an array of tasks. Keeping everyone up-to-date when these protocols change adds to this challenge.
- Safety protocol navigation: Each work process and piece of equipment have unique safety hazards, making it challenging to maintain consistency in safety protocols while accounting for these intricacies.
- Correlation with labor shortages: While establishing a direct cause-and-effect relationship can be complex, the correlation between labor shortages and this increase in accidents and injuries cannot be ignored. Labor shortages often result in longer working hours for the existing staff, leading to fatigue, burnout, and a higher likelihood of making mistakes that could result in accidents.
- Increased risk due to rushed training: When new workers are hired to fill these labor gaps, the urgency to get them working can sometimes result in rushed or inadequate safety training. This leaves these new workers, who are already unfamiliar with the specific hazards of their new workplace, at an even higher risk of accidents.
- Pressure and stress impacting safety: Labor shortages also create a heightened sense of pressure and stress among the workforce, which can further compromise safety. Workers under stress are more likely to cut corners, forget protocols, or make decisions that put them and their colleagues at risk.
Workplace Safety is Personal
- Individual lives are at stake: Safety isn't about checking boxes or avoiding penalties; it's about the lives and well-being of individual people. Employers must be committed to prioritizing the safety of their workforce.
- The weight of responsibility: For safety officers, managers, and CEOs, ensuring workplace safety can feel overwhelming or even impossible, especially when the tools and methods available seem inadequate.
The Shortcomings of Traditional Safety Training
- Ineffectiveness of traditional methods: Conventional safety training, a mix of manuals, lectures, and videos, is too general, and impersonal, and doesn’t engage and educate employees effectively. This is a serious concern because research shows that 40% of employees will leave within one year if they are not properly trained.
- Different learning styles: Traditional training rarely caters to different learning styles or the complexity of practical, hands-on tasks, leading to information gaps, misunderstandings, and incidents.
- Training challenges: Bridging the gap between theoretical knowledge and practical application in safety training is a crucial challenge, which can contribute to information loss, misunderstandings, and accidents.
Keeping Pace with Rapid Workplace Evolution
- Rapidly evolving workplace: Changes in machinery, software, or regulations require constant updates to training materials. Traditional models need help to keep up with this pace, making updates slow and inconvenient.
- Evolving safety standards: Safety standards are constantly evolving, and failing to communicate these changes effectively to the workforce and retrain employees on time can be costly.
- Scaling hurdles: Providing consistent, high-quality training across multiple locations and shifts is challenging due to resource constraints, geographic distance, and high employee turnover rates.
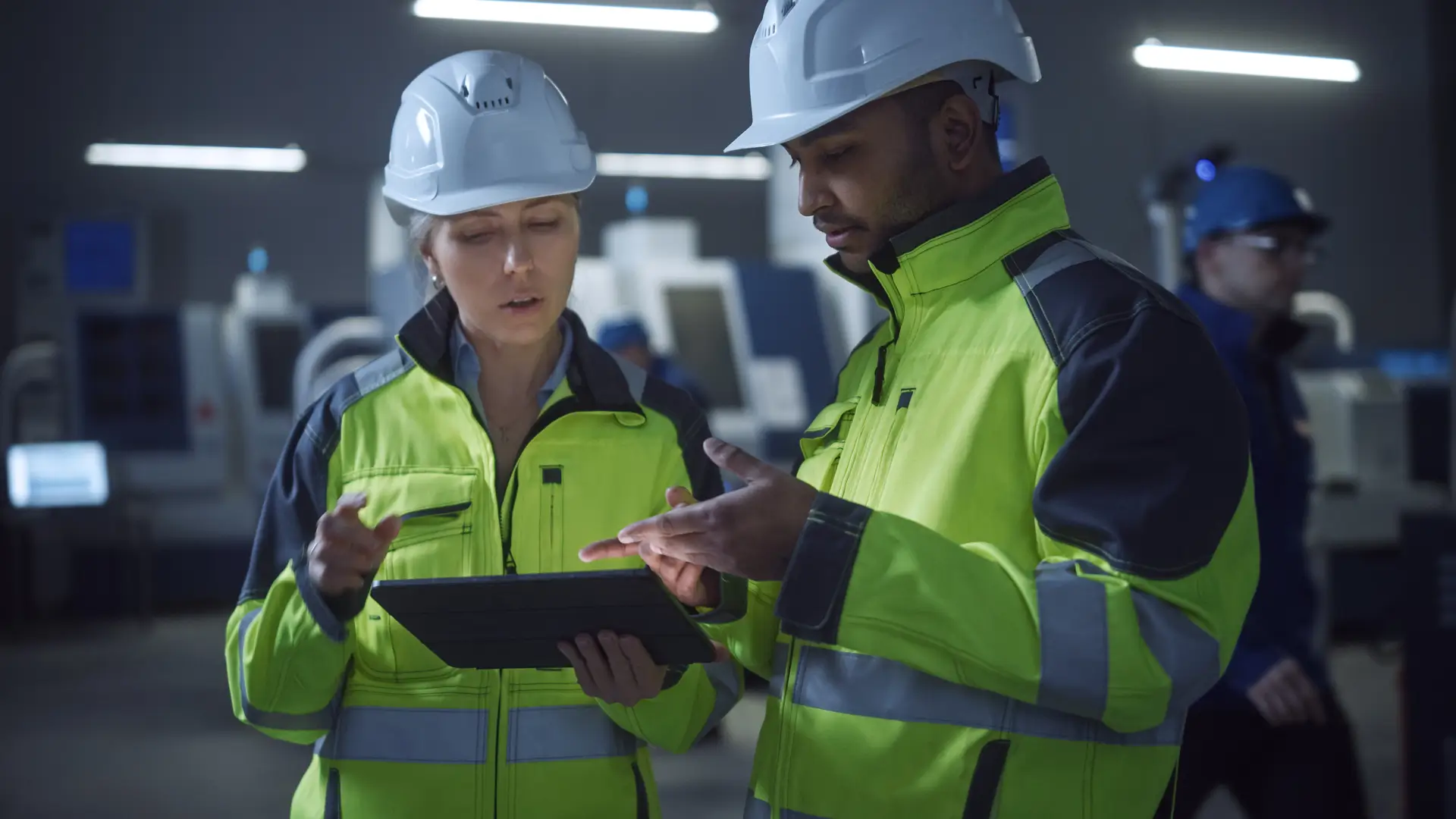
Reinventing Safety Training
DeepHow, an AI-driven video training solution, is reshaping how safety training is delivered and consumed. Immersive videos serve as a robust and engaging tool for training, making complex concepts more tangible and relatable. Whether it's a step-by-step demonstration of machinery operation or a scenario-based safety protocol walkthrough, the video-centric approach of DeepHow brings safety practices to life in a way that text-based or conventional training methods simply cannot match.
The DeepHow platform promotes the repeated revisiting of training content. This consistent reinforcement helps instill the 'how' and the 'why' into the employees' skill sets, leading to a deeper understanding and a more vital commitment to safety practices.
DeepHow leverages advanced AI to provide training that's both effective and engaging. Through its AI capabilities, it delivers content that is personalized, accessible, and easy to comprehend, transforming the once-dreaded safety training into an enriching learning experience.
Key Features of DeepHow
With DeepHow, navigating through the training content is easy. The platform automatically organizes the content and provides smooth navigation options, making the learning experience more efficient and user-friendly.
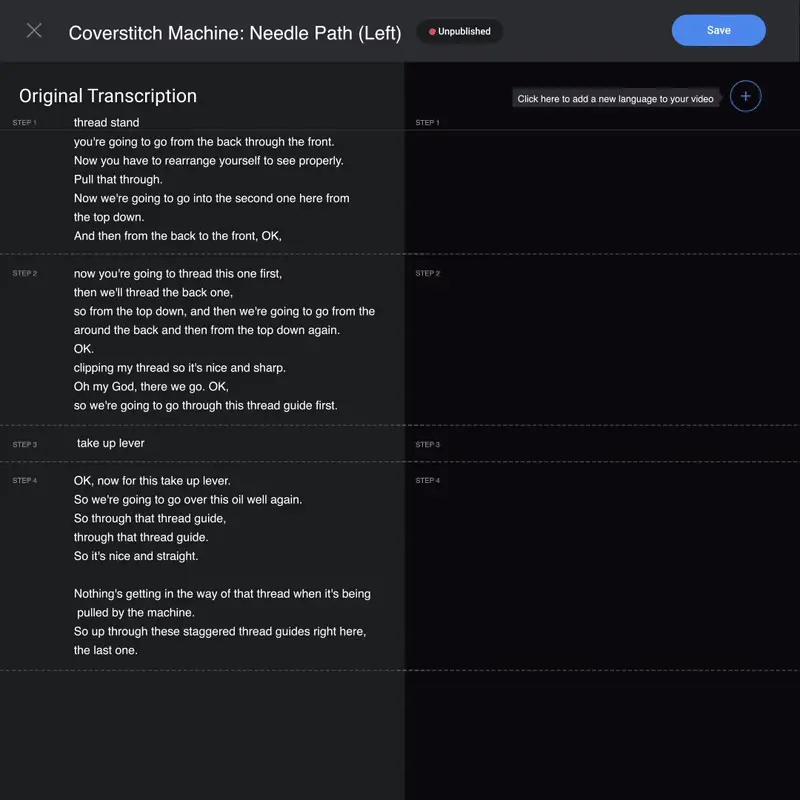
Advanced Search Capabilities: Need to find specific information quickly? No problem. DeepHow's advanced search capabilities allow you to find the exact content you need, exactly when you need it.
Smart Segmentation: DeepHow smartly segments the content into manageable chunks, making it easier for employees to digest and retain information.
Multilingual Translations: DeepHow ensures that language is not a barrier in safety training. Employees can access content in the language they are most comfortable with, improving comprehension and retention. Any video published with DeepHow can have subtitles automatically translatedinto nearly 50 different languages.
Knowledge Preservation: 46% of retiring workers fail to pass their knowledge on to the next generation of employees. DeepHow's platform ensures that critical safety information is preserved and easily accessible. When an employee leaves, their knowledge doesn't leave with them. Instead, it is archived and made available for future employees, reducing the risk of knowledge loss.
Easy Updates: Keeping safety training up to date is crucial as protocols and regulations often change. DeepHow's platform allows for easy updates to content, ensuring that the workforce always has the most current and accurate information.
Continuous Learning and Improvement: DeepHow fosters a culture of continuous learning and improvement. With DeepHow’s easy-to-use platform, employees are encouraged to regularly revisit and reinforce their safety knowledge. Users can scan easily accessible QR codes, allowing immediate access to important safety procedures right at the workstation. With a simple scan of these codes, employees can access relevant safety training videos on demand.
Analytics and Insights: DeepHow provides comprehensive analytics and insights. It tracks employee progress, identifies areas of improvement, and provides valuable feedback, helping organizations to continuously enhance their safety training programs.
Addressing Multiple Factors of Safety Training
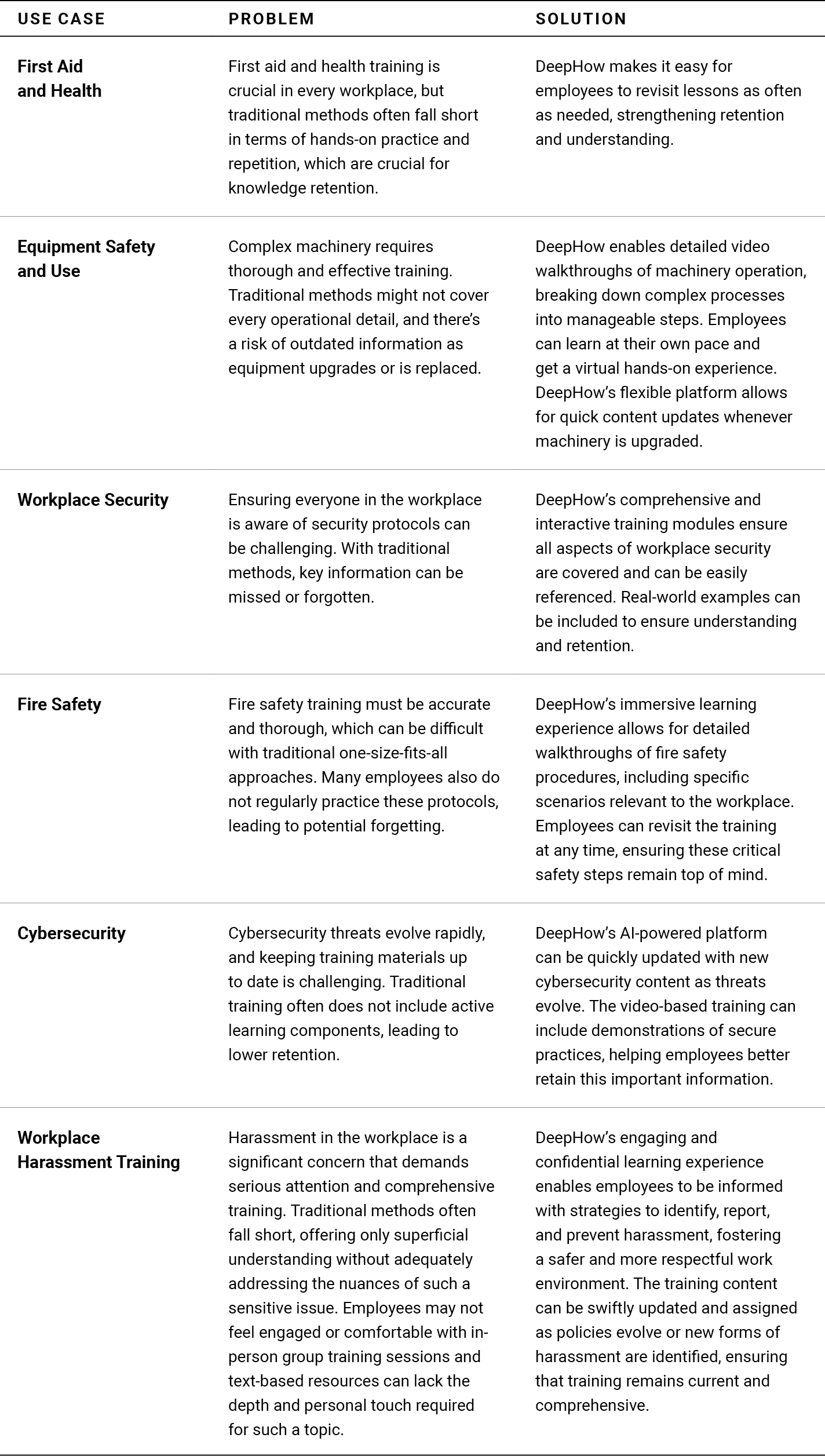
Industry-Specific Applications
To fully appreciate the transformative power of DeepHow's comprehensive, AI-powered training, it's essential to explore how it can be applied in various real-world scenarios. We've compiled industry-specific applications illustrating each sector's unique problems and how targeted training can address these challenges. A wide breadth and depth of issues are mitigated through informed training. So, let's explore how the right training can significantly enhance safety and efficiency across these diverse fields.
Manufacturing
- Ensuring quick response to emergency situations by understanding shut-off procedures for machinery.
- Reducing breakdowns and accidents through routine maintenance and inspections of manufacturing equipment.
- Implementing safety protocols specific to each role, such as emphasizing the importance of lock-out/tag-out procedures for machine operators.
Construction
- Preventing falls and structural collapses by mastering scaffold erection and dismantling procedures.
- Avoiding back injuries by learning the correct method of lifting heavy objects.
- Operating heavy machinery like cranes or excavators safely by understanding their operating procedures.
Healthcare
- Reducing the spread of infectious diseases by adopting proper hand hygiene.
- Preventing cross-contamination by correctly applying and removing PPE.
- Mitigating the risk of healthcare-associated infections through correct methods for cleaning and disinfecting patient rooms.
Food Manufacturing
- Preventing foodborne illnesses through thorough cleaning and sanitizing of food processing equipment.
- Managing allergens and preventing cross-contamination by adhering to proper procedures.
- Ensuring food safety and quality through correct handling and storage of raw materials.
Chemical and Pharmaceutical Processing
- Preventing chemical accidents by following correct procedures for safely storing and handling different chemicals.
- Responding correctly to chemical spills and leaks.
- Operating chemical processing equipment safely by adhering to proper procedures.
Transportation and Logistics
- Reducing the risk of accidents through safe driving techniques.
- Preventing injuries during cargo handling by following correct procedures for loading and unloading.
- Ensuring the safe operation of warehouse equipment such as forklifts and pallet jacks.
Impacting Real-World Safety: Customers Speak
When it comes to the value and impact of DeepHow on industry safety standards, nothing is more persuasive than the experiences of the professionals who have incorporated it into their work environments. Here are insights from experts who have seen first-hand the benefits of DeepHow.
An industry-leading Digital Manufacturing Architect shared: "The team started making videos around potential safety incidents that were happening and the corrective actions. That just sparked and set off the lightbulbs across the global employee health and safety environments. Nothing got these people more excited than DeepHow. I had a robot dog and they were still more excited about DeepHow and seeing how we used it and how it can be used."
At Stanley Black & Decker, the Director of Digital Performance revealed: "Our initial use case was really just for ‘upskilling’ our employees and it evolved into a whole plethora of different use cases. One of the exciting ones is our health and safety teams globally have rolled out standard health and safety training to all 40,000 of our makers using DeepHow exclusively. So it’s been a really powerful tool for helping to make sure we’re keeping people safe in their day-to-day."
At a leading biotechnology company, the Head of Learning shared: "We’re trying to change the model and bring a fresh perspective of how we present information to the people who do the work that supplies our patients with potentially life-saving drugs and one of the things we’re working on is leveraging technology to remove the barriers to access technology. We’re working on a project and part of that project is creating interactive SOPs. Training is in the flow of the work so people can access their information. The idea of using paper on the floor doesn't really align with how we want to maintain the cleanliness and sterility of our facilities.
A touch-enabled tablet that allows you to go through your SOP, you’re presented with risk-relevant information about safety, product quality, about asset management so you don't break the equipment in the process of doing the work… and also see demonstration videos layered into those high risk, high complexity tasks. DeepHow allows us to do this in a very light, efficient, and quick manner where it used to take us weeks and weeks to generate the video, only to find out that the process has changed."