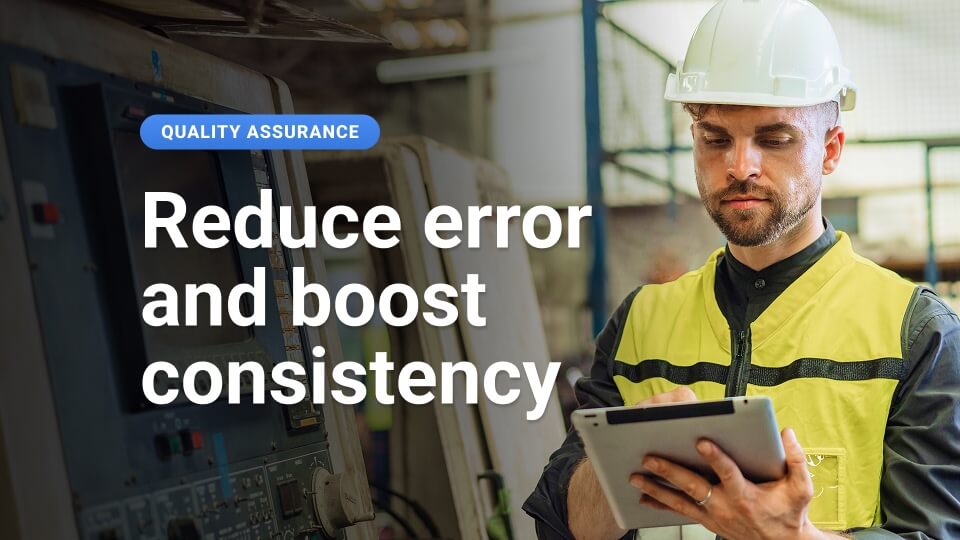
Every manufacturing executive knows that even a single misstep on the production floor can trigger a chain of costly consequences. Human error can lead to lost time, increased expenses, damaged equipment, or even, in severe cases, personal injury. Ensuring that each worker, from the newest hire to the most seasoned team member, has clear, accessible, and accurate guidance is critical to minimizing these risks. One powerful solution? Video SOP (Standard Operating Procedure) training. By standardizing and streamlining training, video SOPs significantly reduce the chances of errors, ensuring consistent performance across shifts, facilities, and roles.
Here’s how video SOP training can be a game-changer for manufacturing operations:
1. Standardize Training Across Teams and Shifts
In manufacturing, inconsistency in task execution can compromise product quality and safety. Video SOPs deliver the same training experience to every employee, eliminating discrepancies that often arise with traditional, text-based SOPs:
- Boost Retention Rates: Research shows that people remember up to 80% of what they watch versus only 20% of what they read. By engaging employees with visual instruction, video training minimizes variability and improves understanding of critical tasks.
- Ensure Consistent Quality: Workers across different shifts and locations can access the same information in an easy-to-understand format, enhancing process uniformity and reducing risks tied to inconsistent SOP adherence.
In addition to standardizing training, video SOPs help teams across shifts maintain alignment and reduce machine downtime caused by inconsistent procedures. By breaking complex tasks into short, accessible videos, employees can independently review and apply precise steps, which minimizes variability and operational delays. This approach is particularly valuable in multi-shift environments where consistent handovers are crucial to maintaining equipment uptime and reducing the need for repetitive in-person training. Video SOPs ensure that every worker has access to the same, up-to-date instructions, helping to keep machines running smoothly and efficiently across shifts.
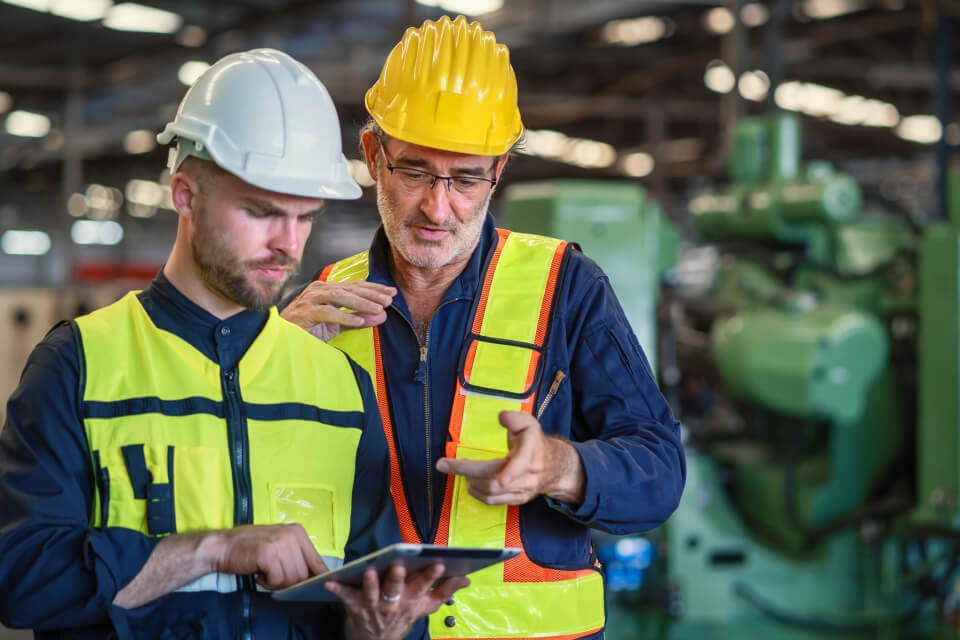
2. Capture and Retain Knowledge from Experienced Workers
With skilled employees retiring and a growing skills gap, manufacturing faces a knowledge retention challenge. Video training platforms like DeepHow make it easy to capture "tribal knowledge", or legacy kowledge—the best practices of tenured workers:
- Faster Onboarding and Upskilling: ABInBev has reduced onboarding times by as much as 80% by giving new employees access to expert knowledge on demand.
- Immediate Access to Guidance: When employees can review video SOPs on the job, they feel more confident performing tasks, leading to fewer mistakes and safer operations.
Video SOP training is a powerful solution for capturing and retaining critical knowledge from experienced employees, which is essential for minimizing errors as they transition out of the workforce. Manufacturing faces a “brain drain” as skilled, tenured workers retire, often taking with them years of specialized know-how that’s difficult to capture with traditional methods. AI-powered video platforms like DeepHow enable manufacturers to document this legacy knowledge by recording experienced employees performing key tasks, preserving practical insights for future hires.
3. Real-Time Data Insights for Continuous Improvement
AI-powered video platforms deliver content and also track performance data to identify improvement areas. This real-time feedback is invaluable for refining training over time:
- Pinpoint Training Gaps: Platforms like DeepHow offer insights into which videos are most viewed or where workers commonly struggle, helping leaders fine-tune training to directly address these issues.
- Adapt Quickly to New Procedures: As processes evolve, AI-supported platforms make it simple to update and distribute new training content, so employees are always following the latest SOPs.
Unlike traditional training methods, which often lack clear feedback mechanisms, platforms like DeepHow track employee engagement and performance, offering executives a continuous view of where training adjustments may be needed.
By monitoring which training videos are accessed most frequently, operations leaders can identify specific skills or procedures that may need clarification or additional support.
These insights allow organizations to proactively address training gaps before they manifest as costly errors on the production floor. For instance, if analytics show a high frequency of views for certain equipment maintenance videos, it may indicate that workers are struggling with that process. Leaders can then adjust the video SOP content or provide supplemental training to ensure smoother operations. This level of data-driven adaptability not only reduces the frequency of errors but also enhances employee confidence and competence by delivering precisely the guidance they need in real time.
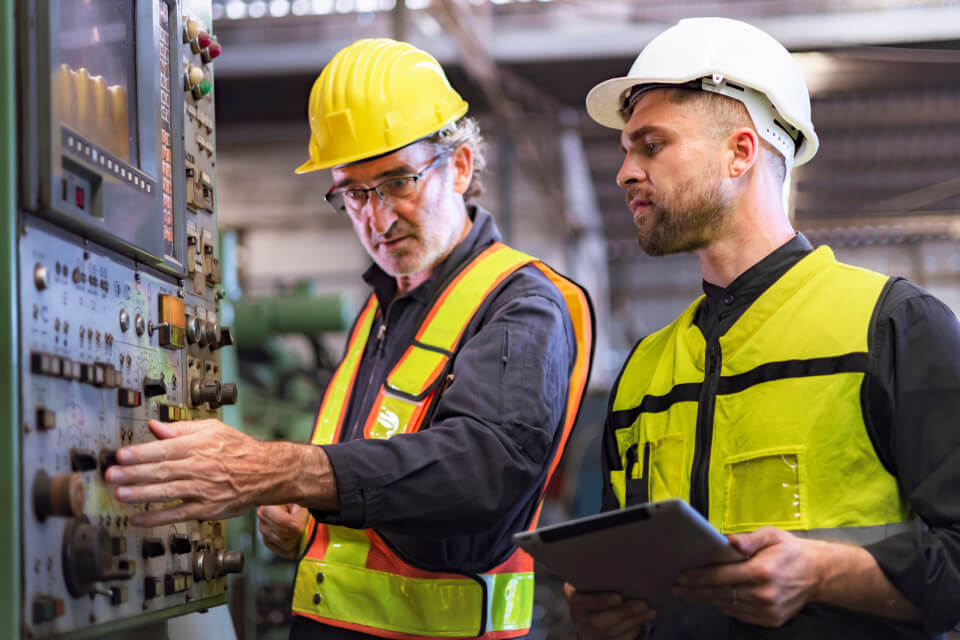
4. Improve Safety and Efficiency, Cutting Down on Costs
Human error doesn’t just affect quality—it can be dangerous and costly. Video SOPs minimize misunderstandings that lead to errors, thereby reducing incidents and improving safety.
- Lower Workplace Accident Rates: Video-based training ensures everyone understands and follows safety protocols, leading to fewer accidents. Manufacturing companies spend more than $140 million each week on non-fatal workplace injuries, which could be reduced with better training.
- Enhance Productivity: Manufacturers that adopt digital training report a 30% increase in operational efficiency, as employees work more confidently and consistently.
Reducing human error through video SOPs not only minimizes product defects but also directly enhances workplace safety, translating into significant cost savings for manufacturers. Errors on the production floor can lead to expensive equipment downtime, damaged goods, and, in worst cases, workplace injuries that impact employee well-being and increase compliance risks. By ensuring that each employee is equipped with clear, precise instructions, video SOPs create a safer environment where procedural errors are minimized, and employees feel more confident and capable of performing their tasks.
5. Foster Accountability and Precision on the Floor
With easy access to video SOPs, employees take greater ownership of their tasks and gain confidence in performing them correctly:
- Empowered Workforce: Video SOPs are readily available for on-demand review, reducing reliance on supervisors and allowing workers to double-check procedures independently as needed.
- Accurate Execution: Video-based training allows employees to see exactly how tasks should be done, setting a clear standard and enabling a culture where precision and accountability are paramount.
AI-powered video SOP training doesn’t just standardize processes—it fosters a culture of accountability and precision that’s essential to high-stakes manufacturing environments. With video training resources readily available, employees can independently verify task steps or safety protocols before execution, reducing dependency on supervisors and minimizing hesitation when performing complex tasks. This empowerment to self-correct promotes greater ownership of tasks and builds confidence, as workers know they are following best practices with up-to-date, accessible resources.
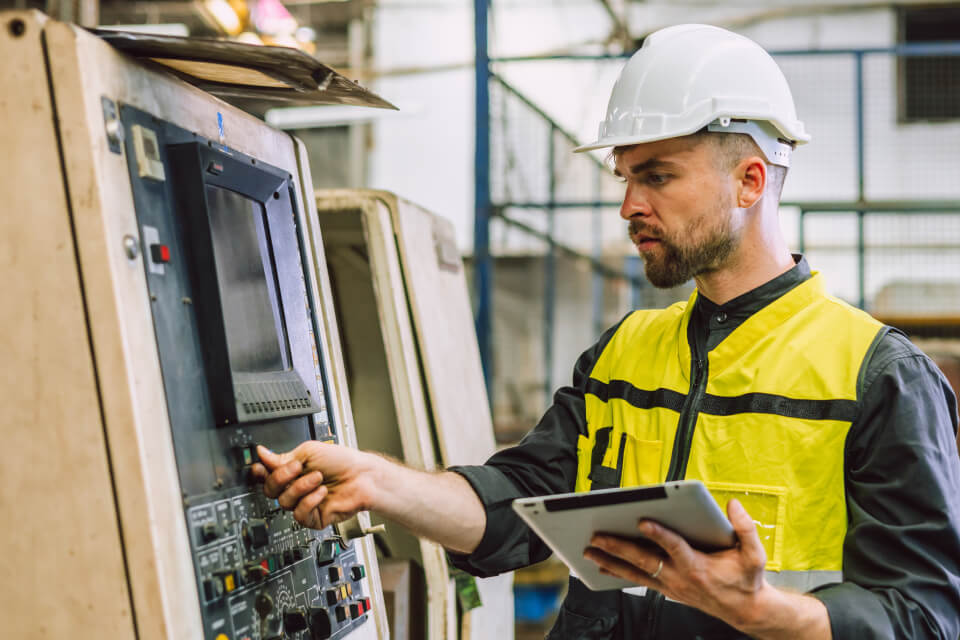
Prioritize Reducing Human Error Now
In manufacturing, reducing human error and increasing consistency is critical for achieving operational excellence. AI-powered video SOP training platforms like DeepHow provide a practical solution by standardizing training, retaining knowledge, and offering real-time insights to keep operations running smoothly. For manufacturing leaders, video training goes beyond reducing errors; it builds a safer, more reliable, and ultimately more profitable production environment.
Investing in video SOP training not only lowers costs and protects employees but also positions your organization for sustained success in an increasingly competitive landscape. Don’t delay. Prioritize reducing human error today by requesting a demo with us.