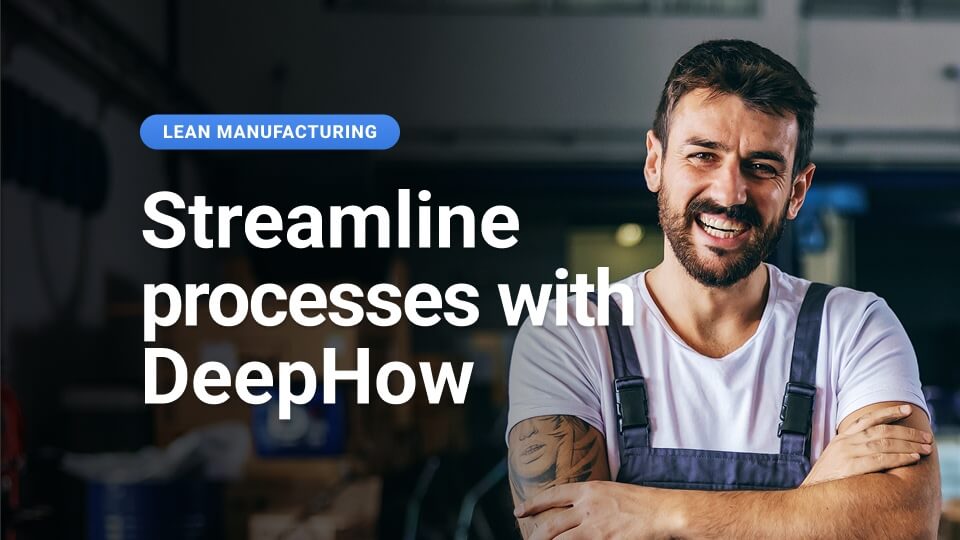
The origin of Lean principles can be traced back to the factory floors of Japan, beginning around 1948, where Toyota pioneered the Toyota Production System (TPS). Faced with limited resources, Toyota’s engineers sought innovative ways to maximize efficiency, minimize waste, and deliver high-quality products just-in-time. This approach focused on continuous improvement, respect for people, and the elimination of non-value-adding activities. These principles laid the foundation that has since transformed industries around the globe, especially within the manufacturing and service sectors.
Standard Operating Procedures (SOPs) play a crucial role in implementing Lean principles, ensuring that processes are consistently carried out to the highest standards. However, traditional SOPs often fall short due to their static nature and reliance on manual documentation. Multimodal SOPs, which can be created using DeepHow Maven, are improving how organizations capture, share, and utilize knowledge.
These advanced SOPs are essential for implementing Lean principles, enabling real-time knowledge capture, minimizing waste, and supporting just-in-time training.
The Essence of Lean Principles
Lean principles focus on creating more value for customers with fewer resources by optimizing workflows, eliminating waste, enhancing efficiency, and fostering a culture of continuous improvement or "kaizen." Respect for people is a core tenet of Lean, extending to customers, workers, suppliers, and society. Lean leaders, working at the “Gemba” or the place where value is created, coach and develop their teams, encouraging them to identify problems and seek improvement opportunities. This approach not only enhances operational efficiency but also promotes personal and professional growth among workers.
The core tenets of Lean include:
- Value — Identify what customers value and focus on those elements.
- Value Stream — Mapping all steps in the value stream and eliminating non-value-adding activities.
- Flow — Ensuring smooth and uninterrupted workflow.
- Pull — Producing only what is needed when it is needed.
- Perfection — Continuously improving processes to achieve the ideal state of operations.
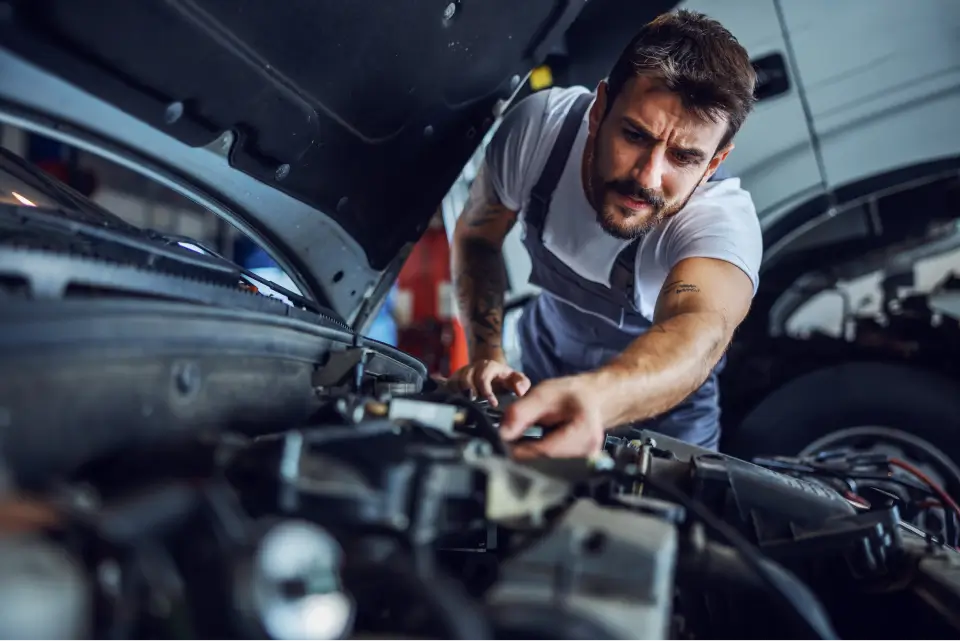
The Evolution of SOPs: From Traditional to Multimodal
Traditional SOPs are typically text-based documents that provide step-by-step instructions. While they are essential for standardizing processes, they often fail to engage employees or convey complex procedures effectively. This can lead to misinterpretations, inefficiencies, and errors.
Multimodal SOPs, on the other hand, integrate various forms of media, including videos, images, audio, and interactive elements. This multimodal approach caters to different learning styles and provides a more comprehensive understanding of processes. DeepHow Maven, a leader in this field, leverages AI to convert video demonstrations into comprehensive, multimodal SOPs, including interactive video SOPs, written/text SOPs, AI-generated summaries, and learning assessments.
This innovative approach ensures that workers can access detailed, engaging, and easily digestible training materials. To illustrate the impact of multimodal SOPs and the integration into Lean processes, consider a manufacturing firm that implemented DeepHow Maven’s solution.
The company faced challenges with inconsistent processes and frequent errors, leading to significant waste and inefficiencies. By adopting multimodal SOPs, they achieved the following results:
- Improved Process Consistency: With clear instructions available to all employees, the organization saw a significant reduction in process variations. This consistency led to higher quality products and fewer defects.
- Reduced Training Time: The time required to train new employees was cut in half. New hires could access interactive training modules on their mobile devices, allowing them to learn at their own pace and refer back to the SOPs as needed.
- Enhanced Knowledge Sharing: The firm’s employees began using the real-time knowledge capture feature to share tips and best practices. This collaborative approach fostered a culture of continuous improvement and innovation.
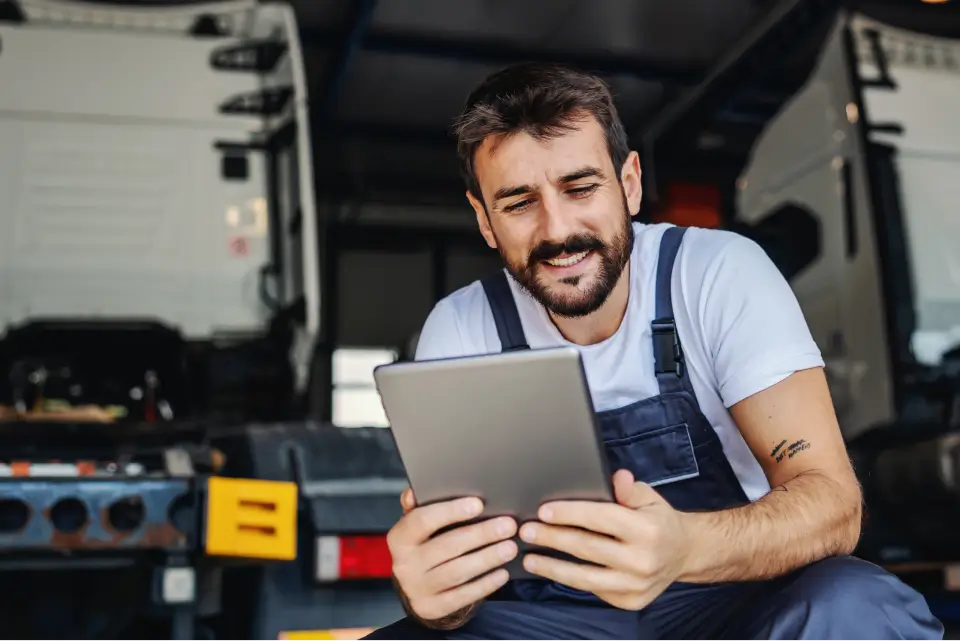
Real-Time Knowledge Capture and Dissemination
One of the significant challenges in Lean implementation is capturing and disseminating expert knowledge across the workforce. Traditional methods of knowledge transfer, such as manuals and classroom training, are often inefficient and fail to keep pace with rapidly changing industry standards. Traditional methods of creating SOPs can be time-consuming and often lag behind actual practice. Multimodal SOPs facilitate real-time knowledge capture. With real-time capture, processes are documented as they occur, capturing nuances and tacit knowledge that might otherwise be lost.
This real-time capture is facilitated by AI-powered tools that can record videos, take snapshots, and generate detailed instructions on the fly, like DeepHow Maven. Employees can use mobile devices to video and document their tasks, which are then processed by DeepHow’s proprietary AI to create a comprehensive SOP. This immediacy ensures that the knowledge is fresh and relevant, reducing the risk of outdated procedures leading to inefficiencies or errors.
Disseminating this knowledge is equally crucial. Multimodal SOPs can be instantly shared across the organization, ensuring that every employee has access to the latest information. This is particularly beneficial for large organizations with multiple locations, where consistent communication and training can be challenging. Multimodal SOPs can also be distributed to various teams and departments within an organization.
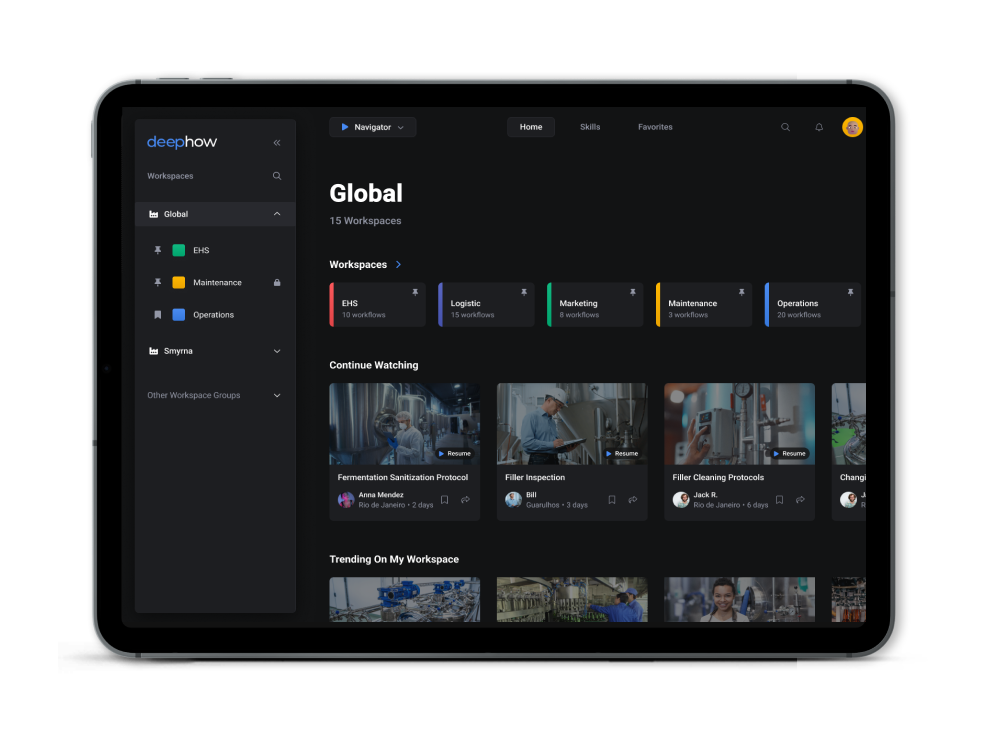
Reducing Waste Through Optimized Processes
AI-driven tools are exceptional at analyzing vast amounts of data to identify inefficiencies and areas for improvement. In Lean manufacturing operations and services, this capability is crucial for optimizing processes and reducing waste. Waste reduction is a fundamental goal of the Lean process, and multimodal SOPs significantly contribute to this objective. There are several ways in which they achieve this:
- Eliminating Knowledge Silos: In many organizations, valuable knowledge is often trapped within departments or individual employees. Multimodal SOPs break down these silos by making knowledge easily accessible to everyone. This transparency leads to more efficient workflows and reduces duplication of effort.
- Minimizing Errors: Traditional SOPs can be ambiguous, leading to errors that result in rework and wasted resources. The clarity provided by multimodal SOPs, with their detailed visuals and step-by-step guidance, minimizes misunderstandings and ensures tasks are performed correctly the first time.
- Streamlining Onboarding and Training: Training new employees can be a significant drain on resources. Multimodal SOPs facilitate quicker and more effective training by providing engaging and comprehensive instructional materials. New hires can get up to speed faster, reducing the time and cost associated with onboarding.
Just-in-Time Training for a Leaner Operation
Just-in-time (JIT) training is a Lean concept that ensures employees receive the training they need exactly when they need it. This approach prevents overtraining and reduces downtime, contributing to a Leaner operation. Multimodal SOPs, like those powered by DeepHow Maven, are ideally suited for JIT training for several reasons:
- Accessibility: Employees can access multimodal SOPs on-demand, from any device, ensuring they have the information they need at their fingertips. This immediacy is crucial for JIT training, as it allows employees to learn and apply new skills in real time.
- Engagement: Traditional training methods can be dull and disengaging. The interactive nature of multimodal SOPs, with videos, animations, and quizzes, keeps employees engaged and enhances retention.
- Customization: DeepHow Maven’s AI-powered platform can tailor training materials to individual needs. For example, it can identify knowledge gaps and provide targeted training to address them, ensuring that employees receive the precise training they need to perform their tasks efficiently.
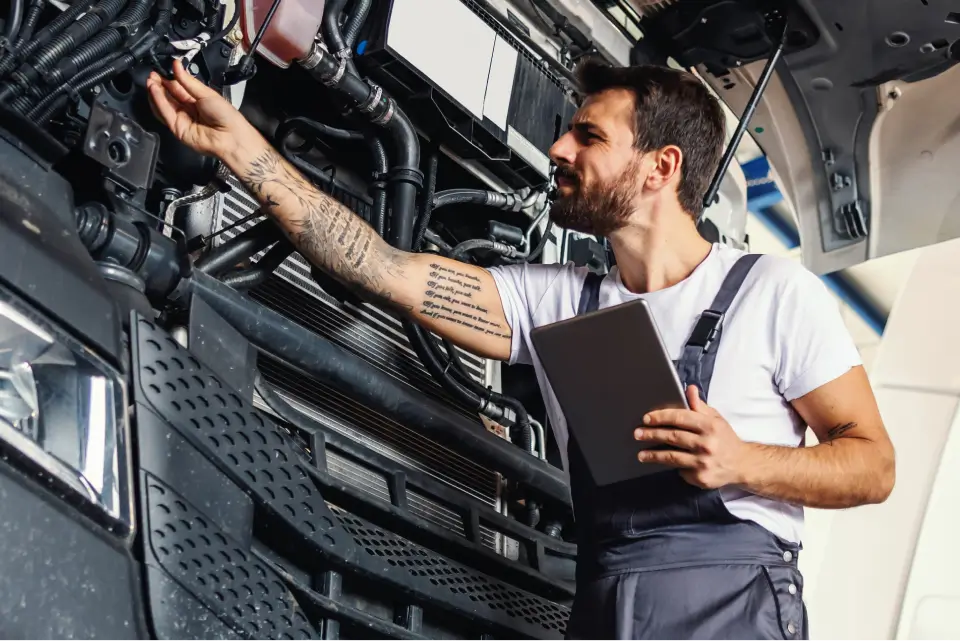
Transforming Knowledge Management and Compliance
Multimodal SOPs are also instrumental in transforming knowledge management and ensuring compliance with industry standards. By integrating AI-driven analytics, these SOPs can continuously monitor and update processes, ensuring that they meet the latest regulatory requirements. This proactive approach reduces the risk of non-compliance and associated penalties. Furthermore, this aligns with the Lean process and principles by eliminating waste in the form of redundant or outdated procedures, ensuring that only the most efficient and effective methods are employed.
Moreover, the detailed records created by multimodal SOPs provide a transparent audit trail, simplifying compliance audits and inspections. This not only enhances operational efficiency but also builds trust with stakeholders and regulators.
The real-time updates and comprehensive documentation ensure that every process is aligned with Lean principles, emphasizing continuous improvement and value creation. This capability to swiftly adapt to regulatory changes without disruption further exemplifies the Lean focus on flexibility and responsiveness in operations.
As manufacturing operations and service industries continue to evolve, the importance of staying compliant with industry standards and regulations cannot be overstated. Multimodal SOPs, such as those offered by DeepHow Maven, provide a powerful tool for achieving this compliance while also enhancing operational efficiency. By leveraging real-time knowledge capture, reducing waste, and facilitating just-in-time training, these advanced SOPs help organizations implement Lean principles effectively.